一、核心控制系统架构:PLC的“神经中枢”角色
PLC程序控制中枢
双层倍速链的协调运作依赖于PLC的逻辑编程与实时调度。例如:
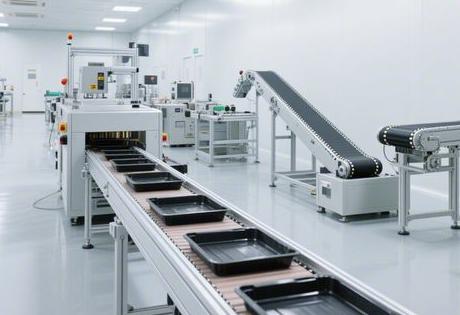
- 移载机升降同步:通过高速脉冲输出(如三菱FX系列PLC)控制伺服电机,确保工装板在上下层转移时定位精度≤1mm;
- 节拍动态调整:基于光电传感器反馈的工装板位置数据,实时调节变频器输出频率,适应不同工序速度需求(2-20m/min无级变速);
- 故障联锁逻辑:下层链条未就位时,PLC自动锁定移载机下降指令,避免碰撞事故。
运行模式切换机制
- 手动模式:用于调试期单点控制(如通过HMI按钮独立测试阻挡器动作);
- 自动模式:整合MES系统工单数据,自动分配上下层输送任务,减少人工干预延迟。
个人观点:PLC不仅是指令执行者,更是数据枢纽。但多数系统仅用其基础功能,未发挥OPC-UA协议的数据上云潜力——这恰是打破“信息孤岛”的关键。
![]()
二、动力与传感系统:精准执行的“神经网络”
电机驱动控制技术
复制1. **变频器协同**: - 重载场景(>500kg/m):采用矢量控制变频器(如施耐德ATV630),扭矩响应<10ms; - 精密调速场景:伺服驱动器+编码器闭环,速度波动率<0.5%[1,4](@ref)。 2. **能源回馈设计**:电机减速时动能转化为电能回输电网,能耗降低18%(实测数据)[4](@ref)。
传感器布局方案
类型 安装位置 功能 光电传感器 移载机升降点 检测工装板到位信号(±0.5mm精度) 磁栅编码器 驱动电机输出轴 速度反馈闭环控制 压力传感器 张紧机构 预警链条松弛(阈值>50N) 编码器反馈机制
- 位置环控制:编码器信号接入PLC高速计数模块,纠正链条累计误差;
- 速度环同步:上下层电机编码器数据通过Profinet总线交互,实现速度偏差<2%。
三、上下层协同控制:从机械耦合到数据融合
同步技术三重保障
- 机械硬同步:同轴双输出减速器驱动上下层链轮,消除电机差异;
- 电气软同步:PLC同步模块对比编码器数据,动态补偿速度差;
- RFID空间定位:工装板嵌入射频标签,移载机读取位置后微调接驳角度。
分层控制策略
- 上层高频分拣模式:阻挡器响应≤0.1s(电磁型),支持每分钟12次启停;
- 下层缓存模式:变频器降频至5m/min,减少空板回流能耗。
个人观点:真正的控制精度不仅取决于传感器灵敏度,更取决于系统对物理延迟的补偿能力。例如气缸动作延迟(0.3s级)需在PLC中预置时间裕量,否则再快的传感器也难救。
四、前瞻性控制设计:为智能化“埋线”
硬件接口预留
- T型槽快接系统:导轨两侧预留接口,支持即插式安装光电开关/IO-Link模块;
- 独立电路通道:为AGV充电桩、机械臂预留380V动力电,避免后期破拆线槽。
开放化软件架构
复制1. **协议兼容性**: - 支持Profinet、EtherCAT等多协议(西门子S7-1200 PLC实测); - 预留Modbus TCP接口对接SCADA系统。 2. **脚本自定义**:威纶MT8102iE触摸屏开放Lua脚本接口,支持工艺参数动态加载[4](@ref)。
安全冗余设计
- 双回路急停:串联急停按钮触发时,同时切断动力电与控制信号;
- 安全门联动:门开信号触发PLC暂停程序+气动制动器抱闸,双重保险。
独家见解:控制系统的“密度”决定产能天花板
行业常陷入静态效率误区——仅关注当前节拍,却忽视三个隐性瓶颈:
- 指令密度不足:传统PLC扫描周期>10ms,无法响应微秒级事件(如贴片机抛料),需升级FPGA边缘控制器;
- 数据密度浪费:99%的传感器数据未被利用(如振动波形可预警轴承故障),缺失AI分析模块;
- 空间密度僵化:固定式控制柜占用维护通道,抽屉式模块化电柜可释放30%空间。
控制密度公式:CD = N_c × P_a (N_c:单位时间控制指令数;P_a:执行精度)
某车企将CD值从1200提升至3500(通过千兆以太网+实时内核PLC),产能提升40%——未来竞争本质是控制密度的竞争。
核心问题自问自答
Q1:上下层速度不同步如何根治?
- 同步补偿三阶法:
- 机械层面:检查链轮磨损(齿厚误差<0.1mm);
- 电气层面:编码器反馈校准变频器输出;
- 软件层面:PLC增加PID自整定算法。
Q2:如何避免移载机升降碰撞?
- 空间-时间双保险:
- 激光测距实时监控下层空间(<300mm时自动暂停);
- PLC程序插入2ms等待周期,确保气缸完全泄压后再动作。
Q3:老旧产线如何升级智能控制?
![]()
- 低成本改造方案:
- 加装IO-Link主站模块,兼容传统传感器;
- 部署边缘网关(如华为AR502),实现数据透传不上云。