## 一、立体输送架构的空间革命
双层倍速链线通过垂直循环设计颠覆了传统产线布局:
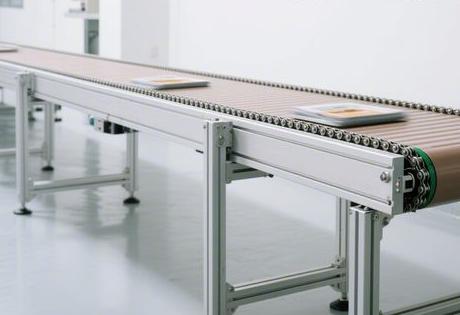
- 上层输送层:承载工装板执行装配任务,工位间距可压缩至2.5米
- 下层回流通道:专用于空工装板无干扰返回,减少40%无效行程
- 顶升平移系统:气缸驱动+双导轨结构实现工装板跨层转移,重复定位精度±0.1mm
这种设计让同等面积厂房的工位密度提升30%-50%。以长城汽车仪表台产线为例,采用光良定制的双层倍速链后,在缩减37.5%占地面积的同时,工位数量反增25%,年产能提升至18万台。
## 二、定制全流程的五大关键阶段
阶段1:需求精准锁定
场景化需求分析需关注:
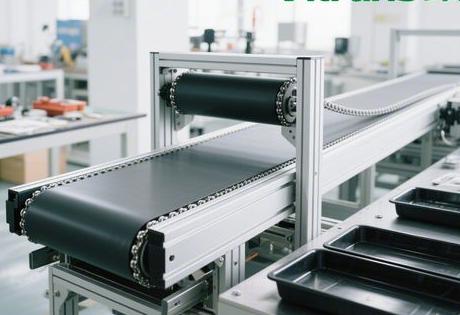
- 负载特性:汽车部件需承载2吨以上重载(淬火合金钢链条),而3C电子通常≤500kg(工程尼龙链条)
- 环境适配:医药行业要求316L不锈钢材质耐受酒精消毒,电子车间需防静电设计(电阻≤10⁶Ω)
- 功能扩展:预埋RFID接口、机器人对接坐标等未来升级需求
案例教训:某锂电池厂因未预留AGV接驳口,后期改造费用超初始投资30%
阶段2:模块化设计实战
图片代码graph LR A[布局规划] --> B{空间限制?} B --厂房高度<5m--> C[紧凑型双层布局] B --平面充足--> D[单层环形方案] C --> E[驱动系统选型] D --> E E --重载场景--> F[3倍速链+5kW双电机驱动] E --轻载高速--> G[2.5倍速链+伺服变频] F --> H[控制系统] G --> H H --基础功能--> I[PLC+触摸屏] H --智能工厂--> J[集成MES+IoT模块]
(数据来源:光良智能2025年定制案例库)
阶段3:制造与验证的硬标准
- 核心部件加工:链轮齿形加工达IT7级精度,导轨直线度误差≤1mm/m
- 负载测试:72小时连续满载运行,记录电机温升(ΔT≤15℃)、链条伸长率(≤0.3%)
- 防错设计:安全光幕+急停双回路控制,响应时间<0.5秒
行业痛点突破:通过激光对中仪校准,解决长距离输送(>40m)的跑偏问题,使故障率降低60%
## 三、选型决策的黄金法则
法则1:材质与负载的匹配公式
场景 | 优选方案 | 避坑指南 |
---|---|---|
汽车/重工(>1吨) | 全钢链条+淬火滚轮 | 避免使用3倍速链,超载30%时断链风险增50% |
电子/家电(≤500kg) | 工程塑料链+自润滑轴承 | 湿度>70%环境需防静电涂层 |
食品/医药 | 316L不锈钢+密封盖板 | 润滑脂需符合FDA标准 |
法则2:速度与精度的平衡艺术
- 精密装配场景:采用伺服闭环控制,S型加减速曲线(加速度≤0.5m/s²)
- 高速分拣场景:2.5倍速链+变频电机,速度范围5-15m/min
- 积放功能关键:阻挡器间隙严格控制在0.1-0.3mm,过紧导致倍速失效,过松引发定位超差
实测数据:某手机贴片线通过伺服定位改造,将偏移率从1.2%降至0.05%
法则3:成本与交期的博弈策略
- 标准化模块:选用铝型材导轨(118 * 100规格)等通用件,缩短交期至15天
- 成本优化点:驱动单元占比总成本35%,国产优质电机(如安川)可替代进口品牌
- 隐性成本预警:忽视自润滑设计将导致年维护成本增加¥8万/千米
## 四、智能升级的三大演进方向
-
数字孪生体监控
在滚轮嵌入微应变传感器,实时监测链条张力波动,预警过载风险(误差率<5%) -
混合驱动架构
基础输送采用传统电机,顶升机构集成直线电机,定位精度跃升至微米级 -
自适应倍速比
研发可变径滚轮结构,通过液压调节实现在线倍速切换(2.5X↔3X),换产时间缩短80%
个人预判:2027年30%高端产线将采用“IoT+混合驱动”架构,虚拟调试技术使投产周期压缩40%
## 自问自答:定制核心疑虑破解
Q1:定制周期通常多久?哪些环节最耗时?
A:常规项目需45-60天,关键耗时点在:
- 方案确认(7-10天):客户需求反复变更导致
- 机械加工(15天):链轮齿形精加工占60%工时
- 联调测试(10天):建议采用模块化预装缩短此阶段
Q2:重载场景为何慎用3倍速链?
A:3倍速链的滚轮-滚子直径比更大,超载时应力集中于链板铰接点。实测数据表明:当负载超标30%时,3倍速链的断链风险比2.5倍速链高50%
Q3:如何降低长期维护成本?
A:实施“三防一智”策略:
- 防尘:加装密封盖板,粉尘环境寿命延长3倍
- 防磨:每月检测滚轮-滚子间隙(>0.1mm)
- 防锈:潮湿环境用锂基耐水油脂(100℃粘度≥46mm²/s)
- 智能预警:IoT平台实时推送轴承温升异常
Q4:模块化设计真能降低成本吗?
A:短期增加10%投入,长期降低30%成本——模块化使新增工位改造成本<¥3万,且停产时间缩短至8小时