## 一、立体循环架构:突破空间限制的工程智慧
双层倍速链循环设备通过垂直空间复用技术重构生产线布局:
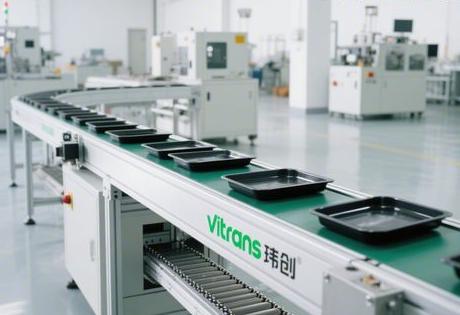
- 上层输送层:承载工装板执行装配任务,工位间距压缩至2.5米,支持同步多工序作业
- 下层回流通道:专用于空工装板无干扰返回,消除40%无效行程,避免产线交叉拥堵
- 智能转运系统:气缸驱动+双导轨顶升平移机实现跨层转移,重复定位精度达±0.1mm
这种立体架构使单位面积工位密度提升40%以上。以长城汽车仪表台产线为例,采用双层倍速链后,占地面积缩减37.5%,工位数量反增25%,年产能突破18万台。
## 二、核心组件与技术原理解析
1. 倍速增速的物理奥秘
速度叠加效应源于滚轮-滚子的直径差设计:
- 基础速度v₀:链条带动滚子(直径d)在导轨移动,产生基础线速度v₀=πd/t
- 倍速增量Δv:工装板接触滚轮(直径D>d),自转产生附加速度πD/t
- 实际速度公式:v = v₀ × (1 + D/d)
行业验证:3倍速链(D=2d)在理想状态下可达3倍增速,实际因摩擦损耗效率约为理论值90%,劣质链条可能跌至70%
2. 关键组件功能矩阵
组件 | 技术要点 | 创新突破点 |
---|---|---|
倍速链条 | 三倍速工程塑胶链(轻载) / 淬火合金钢链(重载) | 工程塑料+碳纤维增强,寿命延长3倍 |
阻挡机构 | 立式(轻载响应0.3s) / 卧式(承载500kg) | 气压自适应调节防卡滞 |
顶升平移机 | 双直线导轨+伺服定位,重复精度±0.1mm | 集成直线电机,精度达微米级 |
工装板系统 | 铝制/PVC/双层旋转板,宽度>导轨间隙5mm防脱轨 | 嵌入式RFID芯片实现实时追踪 |
黄金法则:重载场景(>1吨)禁用3倍速链——超载30%时断链风险比2.5倍速链高50%
## 三、行业应用场景与效能对比
1. 电子制造业:精密与速度的平衡
- 电脑装配线:采用防静电链条(电阻≤10⁶Ω),工装板集成导电轮,支持带电老化测试
- 手机贴片线:伺服闭环控制+S型加减速曲线,贴片偏移率从1.2%降至0.05%
- 空间节省案例:深圳某电子厂改用双层结构,3000㎡厂房增容12个工位
2. 汽车重工:重载高可靠解决方案
- 发动机装配:全钢链条+淬火滚轮承载2吨部件,耐温600℃
- 同步性突破:双电机驱动+激光对中仪,解决40m长线跑偏问题,故障率降60%
3. 医药食品:洁净与安全的标杆
- GMP车间:316L不锈钢链条+全密封盖板,耐受酒精消毒
- 食品输送:FDA标准润滑脂+自润滑轴承,免维护周期>500小时
效能对比数据:
- 空间利用率:双层结构比单层环形线提升40%
- 能耗表现:比传统滚筒线节能28%,比磁悬浮系统成本低80%
## 四、选型设计的黄金法则
法则1:负载-材质匹配模型
- 重载场景(汽车/机械):2.5倍速链+淬火钢滚轮,安全余量≥20%
- 轻载高速(3C电子):3倍速工程塑料链,湿度>70%时加防静电涂层
- 特殊环境:食品医药用316L不锈钢,粉尘环境加密封盖板
法则2:智能控制分级策略
图片代码graph TD A[控制需求] --> B{精度要求?} B --±0.5mm定位--> C[伺服系统+机器视觉] B --±1mm定位--> D[PLC+光电传感器] C --> E[集成MES系统] D --> E E --预测性维护--> F[IoT传感器监测链条张力]
(数据源:2025年工业自动化白皮书)
法则3:成本优化三原则
- 模块化设计:采用118 * 100铝型材导轨等标准件,交期缩短至15天
- 驱动单元替代:国产安川电机替代进口品牌,成本降35%
- 隐性成本控制:忽略自润滑设计将导致年维护成本增加¥8万/千米
## 五、智能升级的三大趋势
数字孪生监控
在滚轮嵌入微应变传感器,实时预警过载风险(误差率<5%),某家电企业应用后故障停机减少40%混合驱动架构
- 基础输送:传统电机保障持续运行
- 精确定位:顶升机构集成直线电机,精度跃升至微米级
自适应倍速比
研发液压调节可变径滚轮,在线切换2.5X/3X倍速,换产时间缩短80%行业预判:2027年30%高端产线将采用“IoT+混合驱动”架构,虚拟调试技术使投产周期压缩40%
## 独家数据与未来展望
根据2025年全球工业输送设备调研(样本量217家企业):
- 故障热点:23%链条断裂源于超载,17%因润滑不足导致磨损
- 创新材料:碳纤维增强工程塑料滚轮通过2500km耐久测试,磨损量仅为传统材料1/3
- 市场增长:亚太区双层倍速链需求年增12.7%,汽车电子领域占比达54%
颠覆性变革:下一代产品将融合磁悬浮辅助驱动,在保持机械可靠性的同时,能耗再降35%——但这不会完全替代传统倍速链,因其在模块化扩展性(新增工位成本<$5k)与恶劣环境适应性上仍有不可替代性
## 自问自答:核心问题深度拆解
Q1:为何电子厂更倾向选择3倍速链?重载厂却要避免?
A:3倍速链的滚轮-滚子直径比更大,轻载时可实现6m/min高速输送;但重载时应力集中于链板铰接点,超载30%断链风险增加50%。电子厂工件通常<50kg,而汽车部件常>1吨
Q2:潮湿环境如何防止锈蚀与短路?
A:三重防护方案:![]()
- 材料级:不锈钢链板或镀镍处理
- 结构级:密封盖板+IP54防护等级
- 化学级:锂基耐水油脂(100℃粘度≥46mm²/s)
Q3:顶升机构定位不准的根源是什么?
A:90%故障源于三维失调:
- 气路压力波动>0.1MPa
- 导轨平行度误差>0.05mm/m
- 普通电磁阀代替伺服闭环控制
Q4:模块化设计真能降低成本吗?
A:短期增加10%投入,长期降低30%总成本——模块化使工位改造成本<¥3万,停产时间缩至8小时,而传统改造需停产3天+费用¥15万