核心原理:解密倍速链的机械巧思
自动倍速链输送线的核心在于“低速链条驱动,高速载具运动”的物理设计。其增速机制依赖滚轮(直径D)与滚子(直径d)的直径差:当链条以速度ν移动时,工装板实际速度 V = (D/d + 1) × ν。例如,当D/d=2时,工装板速度可达链条的3倍。这一设计实现了连续输送中的精准暂停——通过气压阻挡器控制工装板停位,误差可控制在±0.5mm内,满足装配、检测等工序的节拍需求。
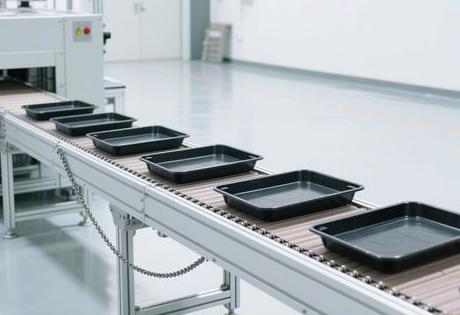
关键组件解析:从滚轮到智能控制系统
一条高效自动倍速链输送线由五大模块协同构成:
-
传动链条与导轨
- 链条选型:轻载线(≤500kg)采用工程塑料滚轮降噪,重载线(≤4000kg)需钢制滚轮;
- 导轨设计:高刚度铝合金型材确保直线度,回程导向装置防止链条卡滞。
-
驱动与调速系统
- 变频电机或伺服电机实现2-20米/分的无级调速,空载段提速至20米/分,装配段降至2米/分以匹配人工操作节奏;
- 双排链轮分散受力,避免单点过载导致的链条断裂。
-
定位与分流模块
- 光电传感器+电动阻挡器实现毫米级停位;
- 顶升平移机、直角移栽机完成工装板的转线、积放,支持多层垂直循环布局,节省厂房空间30%以上。
-
智能控制中枢
PLC系统集成三大功能:- 动态节拍控制:根据传感器数据自动调整速度(案例:某汽车厂产能提升40%);
- 故障自诊断:过载报警、堵料停机;
- OEE(设备综合效率)分析:实时计算停机时间与产能损失。
行业赋能:从汽车装配到医药包装的全场景应用
- 汽车制造:重载倍速链(负载≤4000kg)承载车身焊接,配合顶升旋转台实现多角度装配,节拍压缩至90秒/台;
- 电子半导体:轻载线(负载≤500kg)搭载防静电滚轮,在万级洁净室内输送芯片基板,避免微粒污染;
- 医药包装:全不锈钢链条符合GMP标准,顶升机构实现灌装工位的无菌隔离;
- 锂电池生产:倍速链+直角移栽机组成封闭矩形回路,完成电芯-模组-电池包的自动流转,产能提升50%。
设计挑战:工程优化与成本平衡
企业在部署倍速链时常面临三大矛盾:
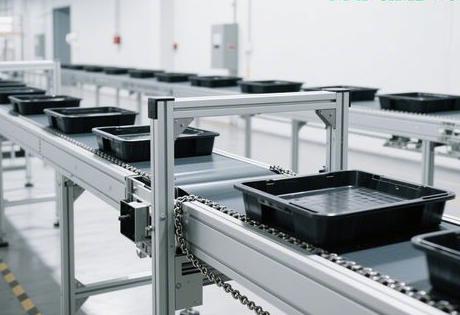
-
增速比与结构限制
理论上D/d比值越大增速越高,但受链条节距制约,滚轮直径无法无限增加。部分企业尝试滚轮内嵌行星齿轮组,增速比提升至4-5倍,但成本激增40%。环境适配性
高温车间需耐热链条(工作温度≥150℃),腐蚀性环境要求镀镍或不锈钢材质,导致造价提高25%-30%。维护成本陷阱
链条每月需润滑保养(高温锂基脂),张紧度偏差>2%即引发跑偏;若忽略减速箱换油(首次3个月,后续每年1次),可能导致电机过载报废。
个人洞见:倍速链技术的未来进化方向
-
模块化设计的产业突围
当前倍速链多为定制化生产,不同厂商的导轨接口、控制系统互不兼容。若推行“乐高式”标准模块(如顶升机构、传感器接口统一化),可缩短交付周期30%,但需头部企业牵头建立行业协议。 -
数字孪生驱动的预防性维护
通过振动传感器+温度探头采集链条数据,可在虚拟模型中预判磨损节点。某试点项目显示,预防性维护使意外停机减少70%,但高精度传感成本仍是普及障碍。 -
与柔性制造的深度耦合
未来倍速链将超越“输送工具”定位,进化为柔性产线的智能协调中枢——例如通过RFID识别工装板物料,自动调度机器人完成分拣装配,实现“零切换”混线生产。
自问自答:倍速链输送线的核心疑问
Q1:为何说倍速链是“效率与精度的双赢”?
A:传统皮带线仅支持匀速输送,倍速链却允许载具高速移动中精准暂停。例如汽车装配线,工件以6米/分输送,遇阻挡器瞬间停位(±0.5mm),装配节拍压缩至皮带线的1/2,精度提升3倍。Q2:企业导入倍速链需哪些配套升级?
A:必须同步改造三环节:- 工装板标准化:统一定位销孔(ISO公差±0.1mm);
- 能源快插系统:气路/电路模块化接口,保障工作站快速接驳;
- MES(制造执行系统)集成:PLC直接对接MES指令,实现动态排产。
Q3:哪些场景应慎用倍速链?
A:两类场景性价比偏低:- 超长节拍产线(如风电叶片装配,节拍>30分钟),输送效率优势无法抵消设备成本;
- 散料无载具运输:矿石、粮食等直接接触滚轮,易导致链条卡死。
结语:隐形引擎的战略价值
自动倍速链输送线正在成为工业4.0的“沉默基石”——它用机械智慧重构了时间与空间的制造逻辑:让物料在流动中被加工,在行进中完成蜕变。当模块化与数字孪生技术逐步成熟,这条“链”将蜕变为智能制造的核心脉络,驱动效率革命从产线延伸至整个工业生态。