## 一、立体循环架构的工程智慧
双层循环倍速链通过垂直空间复用技术重构生产线布局,其核心在于上层生产层与下层回流通道的闭环设计:
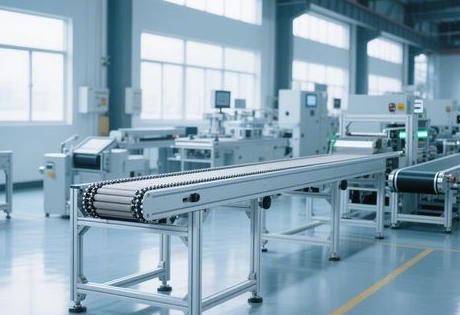
- 上层输送层:承载工装板执行装配任务,工位间距压缩至2.5米,支持多工序并行作业
- 下层回流通道:空工装板通过移载机垂直转运至下层,消除40%无效行程,避免产线交叉拥堵
- 动态调速机制:基于滚轮(D)与滚子(d)的直径差实现倍速效应(公式:v = v₀ × (1 + D/d)),使工装板速度达链条速度的2-3倍
行业验证:长城汽车仪表台产线采用此结构后,占地面积缩减37.5%,工位密度提升25%,年产能突破18万台
## 二、核心组件的协同技术
1. 移载机的精准对接
- 垂直转运:气缸驱动+双直线导轨,重复定位精度±0.1mm,气路压力波动需≤0.1MPa
- 防碰撞设计:RFID定位模块实时校验工装板位置,误差>0.5mm触发急停
- 能耗优化:伺服再生制动技术回收下降势能,节能率≥15%
2. 阻挡机构的智能控制
类型 | 适用场景 | 技术突破点 |
---|---|---|
气动卧式 | 重载(承载500kg) | 气压自适应调节防卡滞 |
电动立式 | 精密装配(响应0.3s) | 压电陶瓷传感器检测微米级偏移 |
黄金法则:阻挡器间隙严格控制在0.1-0.3mm——过紧导致倍速失效,过松引发定位超差 |
3. 模块化扩展接口
- AGV接驳口:预留标准化接口降低后期改造成本30%
- 机器人协同:工装板预埋定位靶标,引导机械臂±0.05mm精度抓取
## 三、行业定制化实战方案
1. 电子制造业:防静电与高精度
- 静电防护:工程塑料链+导电轮(电阻≤10⁶Ω),湿度>70%时加防静电涂层
- 振动抑制:伺服闭环控制+S型加减速曲线(加速度≤0.5m/s²),贴片偏移率降至0.05%
2. 汽车重工业:重载与同步性
- 淬火合金钢链:单点承载2吨,耐温600℃
- 长距防偏:双电机驱动+激光对中仪,解决40m长线跑偏问题,故障率降60%
3. 食品医药业:洁净合规
- 无死角结构:316L不锈钢链条+全密封盖板,耐受酒精冲洗
- 零污染润滑:FDA认证自润滑轴承,免维护周期>500小时
效能对比:
- 空间利用率比单层环形线提升40%
- 能耗比传统滚筒线低28%,成本仅为磁悬浮系统20%
## 四、选型设计的黄金法则
法则1:负载-材质匹配模型
- 重载场景(>1吨):禁用3倍速链!优选2.5倍速链+淬火钢滚轮(超载30%时断链风险低50%)
- 轻载高速:3倍速工程塑料链,碳纤维增强寿命延长3倍
- 特殊环境:粉尘工况加密封盖板,潮湿环境用锂基耐水油脂(100℃粘度≥46mm²/s)
法则2:成本与效率平衡
图片代码graph TD A[需求分析] --> B{空间限制?} B --厂房高度<5m--> C[紧凑型双层布局] B --平面充足--> D[单层环形方案] C --> E[驱动系统选型] D --> E E --重载场景--> F[2.5倍速链+双电机] E --轻载高速--> G[3倍速链+伺服变频]
(数据源:2025年工业自动化白皮书)
隐性成本预警:忽略自润滑设计将导致年维护成本增加¥8万/千米
## 五、智能升级的三大演进方向
- 数字孪生监控
滚轮嵌入微应变传感器,实时预警过载风险(误差率<5%),某家电企业应用后故障停机减少40%- 混合驱动架构
- 基础输送:传统电机保障持续运行
- 精确定位:顶升机构集成直线电机,精度跃升至微米级
- 自适应倍速比
液压调节可变径滚轮,在线切换2.5X/3X倍速,换产时间缩短80%独家预判:2028年将出现“链-机共生体”——倍速链直接嵌入驱动电机,取消机械传动链,能耗再降35%,但需突破永磁体耐温>200℃的技术瓶颈
## 自问自答:工程落地核心问题
Q1:为何汽车厂禁用3倍速链?电子厂却适用?
A:3倍速链的滚轮-滚子直径比更大,重载时应力集中于链板铰接点。实测数据:负载超30%时,3倍速链断链风险比2.5倍速链高50%。电子厂工件通常<50kg,而汽车部件常>1吨Q2:如何解决垂直转运定位偏差?
A:三维校准策略:![]()
- 气路稳压(波动≤0.1MPa)
- 导轨校正(平行度误差<0.05mm/m)
- 伺服阀替代电磁阀
Q3:模块化改造真能降本吗?
A:短期增投10%,长期降本30%——模块化使工位改造成本<¥3万,停产时间缩至8小时,传统改造需¥15万+3天停产Q4:食品线如何避免润滑污染?
A:三重防护:
- 物理隔离:不锈钢迷宫式密封环
- 化学替代:FDA认证润滑脂(含水量<500ppm)
- 智能监测:油脂含水量实时预警