For traditional manufacturing enterprises, in the automation transformation process, the conveyor line is like the production workshop "vascular system" - the right choice can open the production efficiency of any two veins, the wrong choice may become a choke point "thrombosis! ". So, in the face of a wide variety of conveyor lines on the market, enterprises in the end how to choose in order to achieve real cost reduction and efficiency?
I. Comparison of 6 mainstream conveying lines
1.belt conveyor
Advantages: Rubber/PVC/PU material options, can convey bulk materials, cartons, bags, etc., anti-static models can also handle precision electronic components.
Applicable scenes: food processing, electronic product assembly, daily chemical packaging and a series of small or packaged products conveyance.
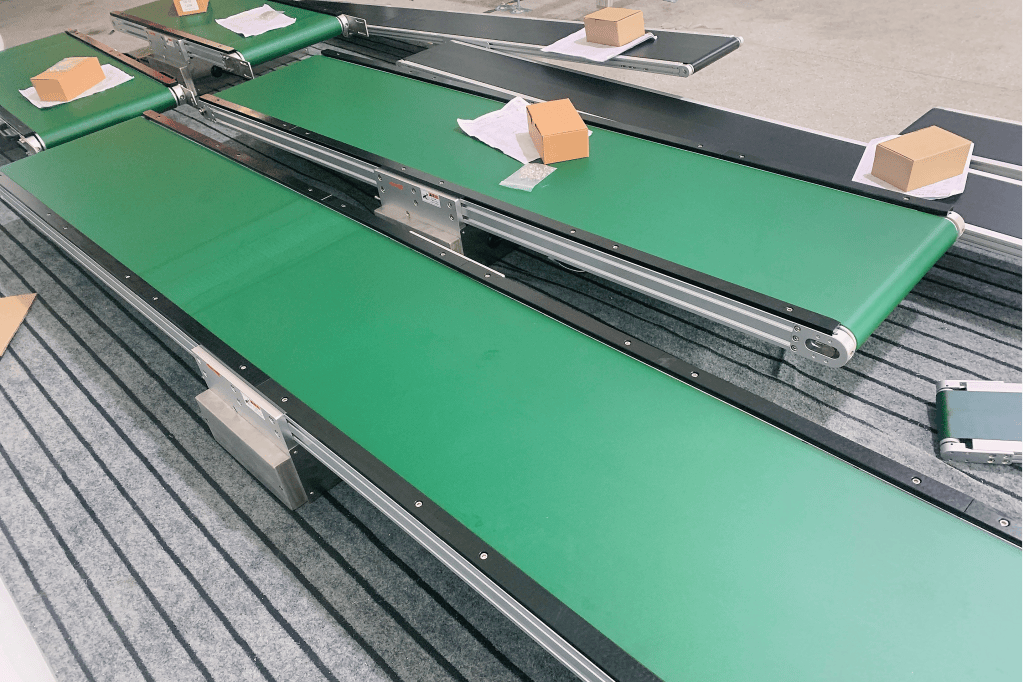
2. Roller conveyor lines
Non-powered models: manual push, suitable for temporary turnaround areas (courier sorting pre-positioning areas)
Power model: can turn at right angles, lifting and shunting, to meet the needs of e-commerce warehousing
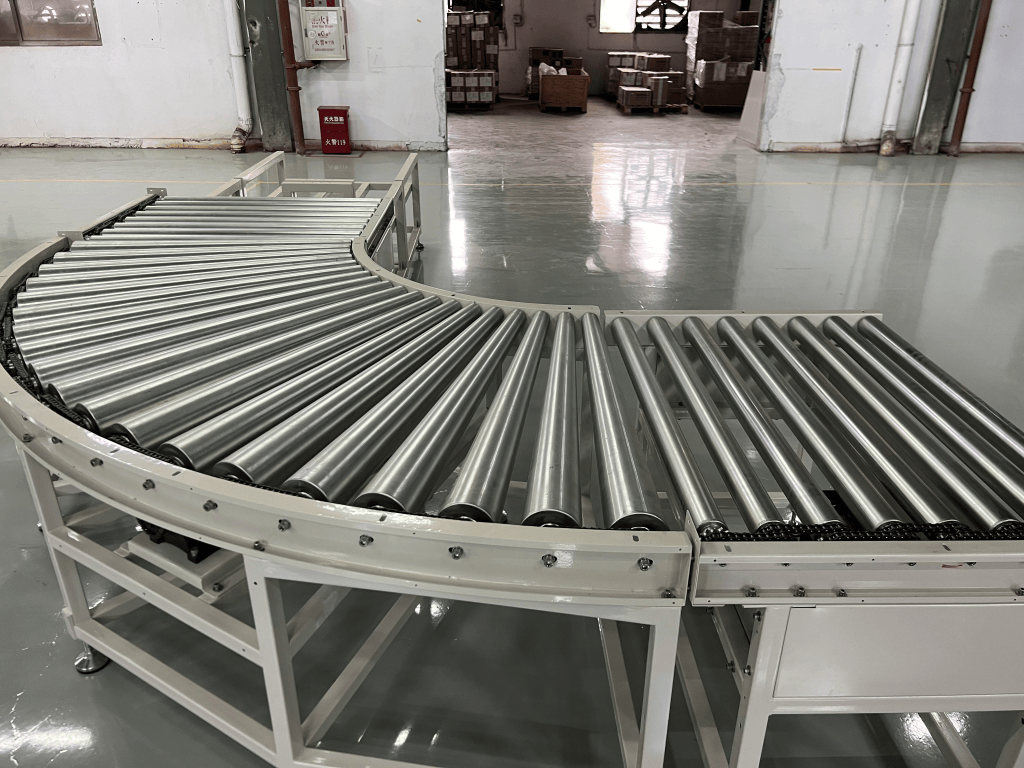
3.Flexible chain plate line
Core features: safe materials, low noise and cleanliness, flexibility and compactness
Application scenarios: food processing (baked goods, beverage filling lines), pharmaceutical production (drug dispensing, medical device assembly lines)
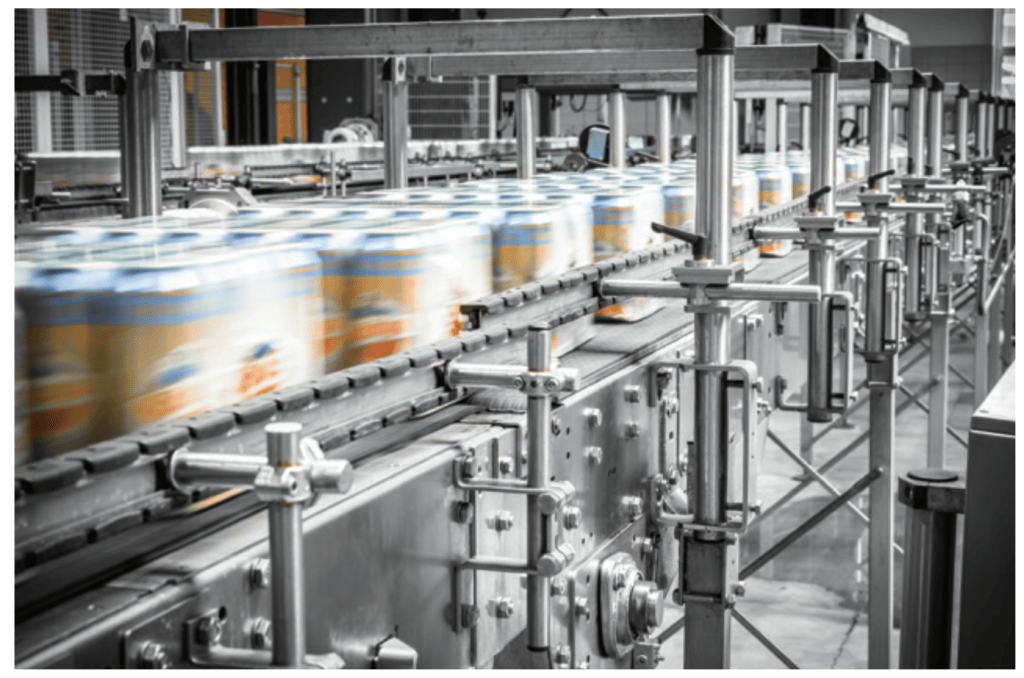
4.Speed Chain Conveyor Line
Advantage: variable speed + precise positioning, but also multiply the efficiency, flexible production, stability, meet the intelligent integration of the
Industry application: Widely used in manufacturing fields that require high-precision, multi-station co-operation, such as automotive assembly, 3C electronic assembly, home appliance production, etc.
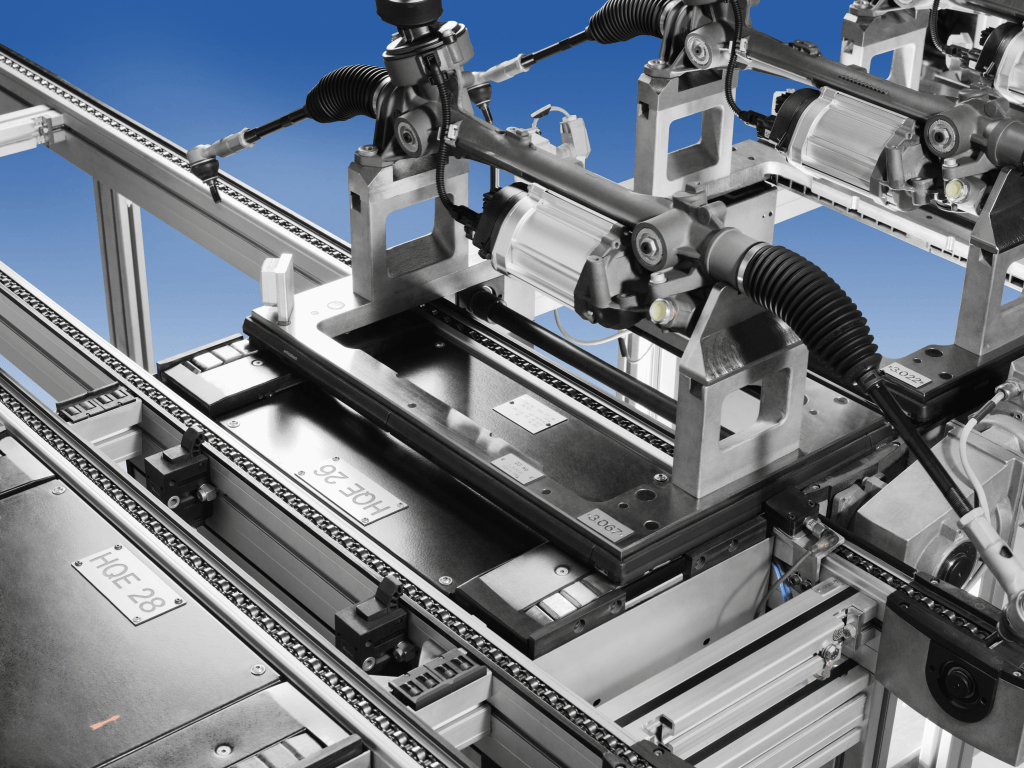
5. Mesh belt conveyor lines
Adaptable: -20℃ cold storage to 200℃ drying oven can be competent
Special applications: sponge production moulding lines, nut roasting lines
6. Overhead conveyor lines
Three-dimensional shuttles: for airborne transport and space saving
Scenario: Suitable for automated conveying of piece goods within and between workshops.
Second, the 5 principles of selection
- Load Capacity: Ensure that the conveyor line has sufficient load capacity to accommodate the weight and size of the material.
- Conveying length and layout: According to the layout and flow of the production process, choose the appropriate length and type of conveying line.
- Conveying speed and efficiency: according to the requirements of production efficiency, choose the appropriate speed of the conveyor line.
- Environmental adaptability: the conveyor line should be able to operate stably in various production environments, including high temperature resistance, corrosion resistance, dustproof and other special requirements.
- Maintenance and costs: Consider the ease of maintenance and cost-effectiveness of the conveyor line to avoid excessive investment and running costs.
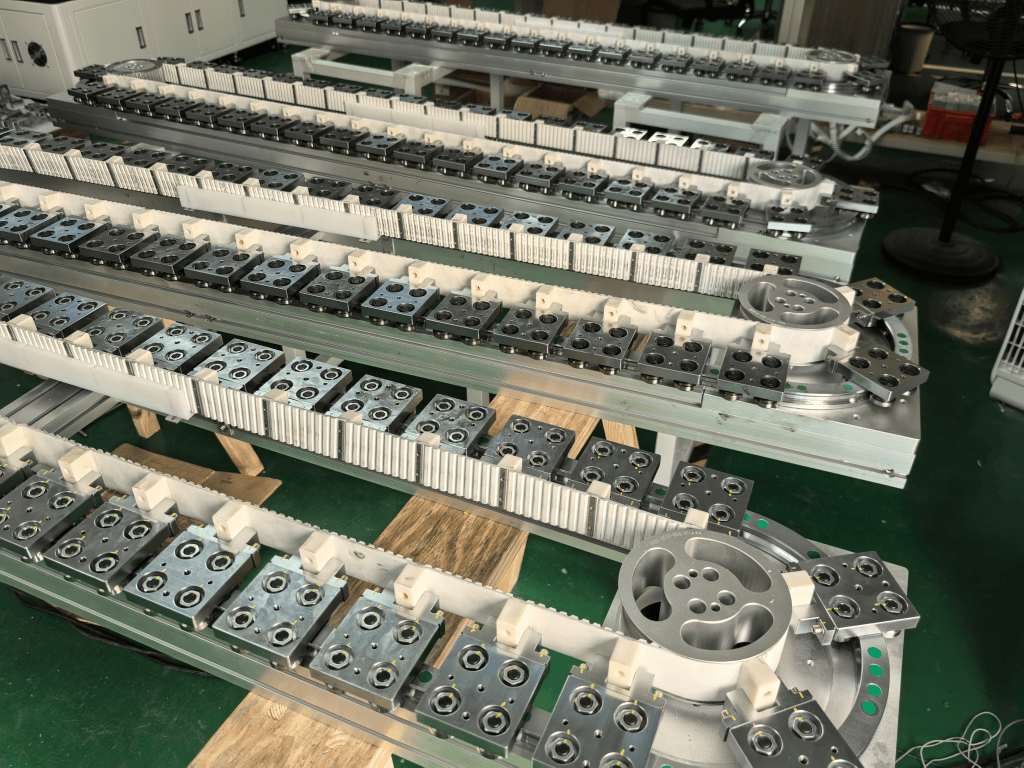
Third, the conveyor line maintenance maintenance of the 5 key points
Regular maintenance and servicing is required to ensure proper operation and prolonged service life of the conveyor line equipment, including:
-Checks the operational status of equipment
-Cleans surfaces and interiors of equipment
-Replacement of worn parts
-Lubricates drive components
-Regular testing and maintenance to detect and deal with faults in a timely manner
Conveying line equipment is one of the important and indispensable equipment in modern manufacturing industry. Through the proper selection and use of conveyor line equipment, you can significantly increase productivity, reduce production costs, improve product quality, and drive innovation and development in the manufacturing industry. Choosing a conveyor line is never a multiple choice question, but a customised equation based on the production process. Expensive may not be the best, the right one is the king.