In the era of intelligent manufacturing, automated conveying system has become the standard equipment of modern factories. In the face of diverse production scenarios, how to accurately match the conveying equipment has become a problem that enterprises must think about. Different industries have different requirements for conveying efficiency, carrying capacity and environmental adaptability, and only through comprehensive evaluation from multiple dimensions can we select the optimal conveying solution. Therefore, we need to comprehensively consider the following factors:
Selection of automated conveying equipmentcharacteristic element
01 Material size
The size of different materials varies significantly, from tiny electronic components to large automotive parts. For example, in electronic production lines, small circuit boards require precisely positioned pallets for conveying, while pallets carrying large car body parts are required in automotive manufacturing. As a result, parameters such as pallet size and belt width of the conveyor must match the size of the material to ensure that the material is stabilised during conveying and avoids shifting or falling.
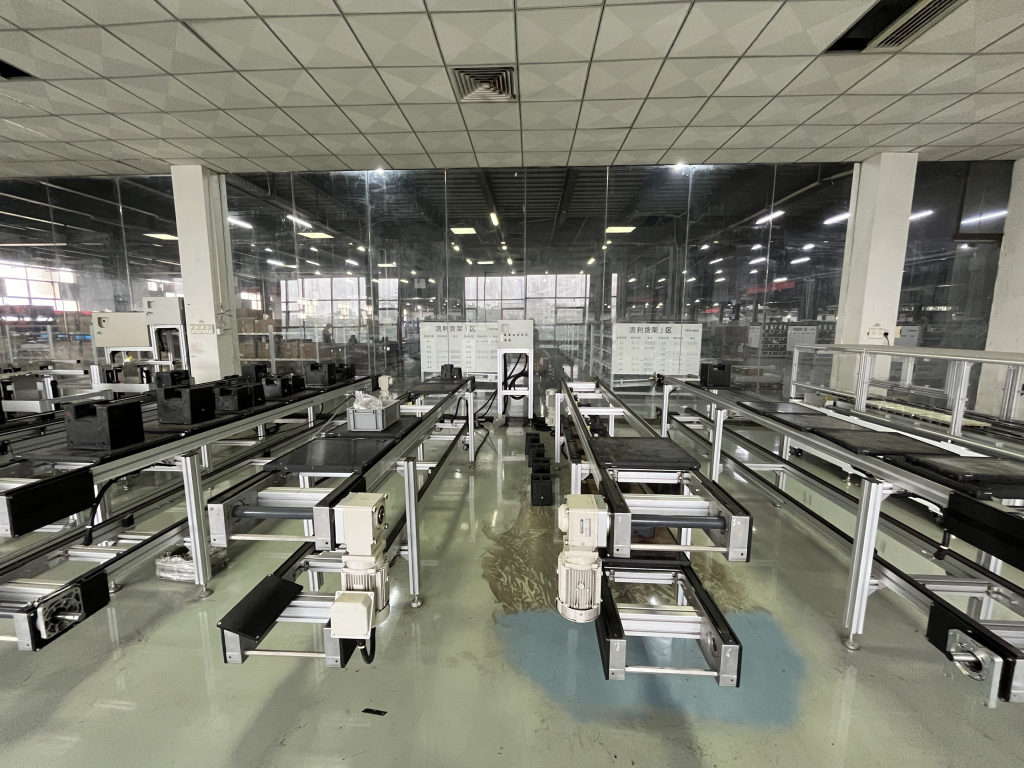
02 Material weight
The weight of the material determines the load capacity requirement of the conveyor. For example, Wei Chuang's products have a load capacity ranging from 60kg to 240kg for pallets, while the Speed Chain Line can carry much heavier weights, from 2200kg for light loads to 4000kg for heavy loads. when selecting the equipment, it is important to ensure that the maximum load capacity is greater than the actual material weight, in order to safeguard the stability of the conveyor and the service life of the equipment.
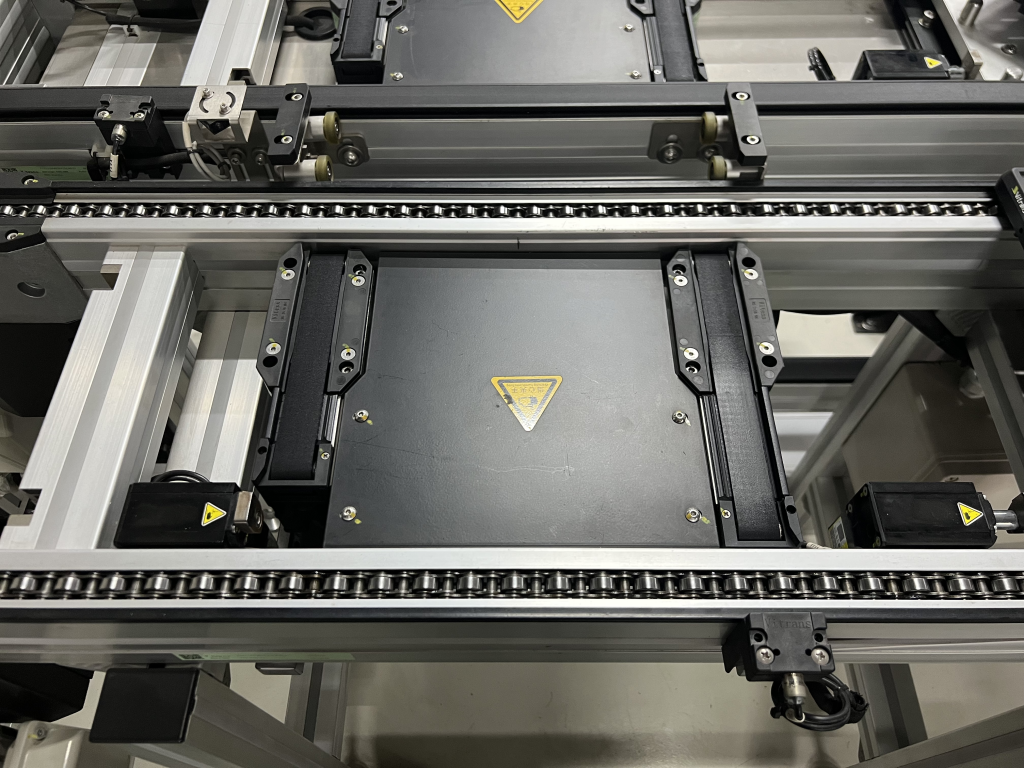
03 Conveyor size
Conveying capacity is a key indicator of line efficiency. For high-tempo production lines, such as those in the 3C electronics industry, conveyors need to be able to convey quickly and continuously.Synchronous belt conveyor lineIt supports forward and reverse operation, the longest single section is 6 metres, and the maximum load of a single section is 60kg, which can meet the needs of small and medium conveying capacity.Flat Belt Conveyor LineWith a maximum length of 25 metres and a maximum load of 250 kg per section, it is suitable for medium conveying capacity scenarios;doubled speed chainThe line is suitable for heavy-duty, high-volume production environments.
04 Conveyor positioning requirements
Highly accurate conveyor positioning is critical to improving production quality. For example, in the semiconductor packaging and testing line, the precise positioning of chips directly affects the quality of packaging. Weitron automation's conveyor positioning accuracy can reach ±0.1mm, which can effectively reduce the adjustment time of the subsequent process, and improve the assembly efficiency and product consistency.
05 Conveying distance
Conveying distance affects the type of equipment and layout. Short distance conveying can choose synchronous belt or flat belt conveying line, while long distance, large load conveying is suitable for speed chain line. Such as lithium battery production line in lithium industry, according to the layout of the workshop and process flow, you need to choose the right length of conveyor line to optimise the production process and reduce the material turnaround time.
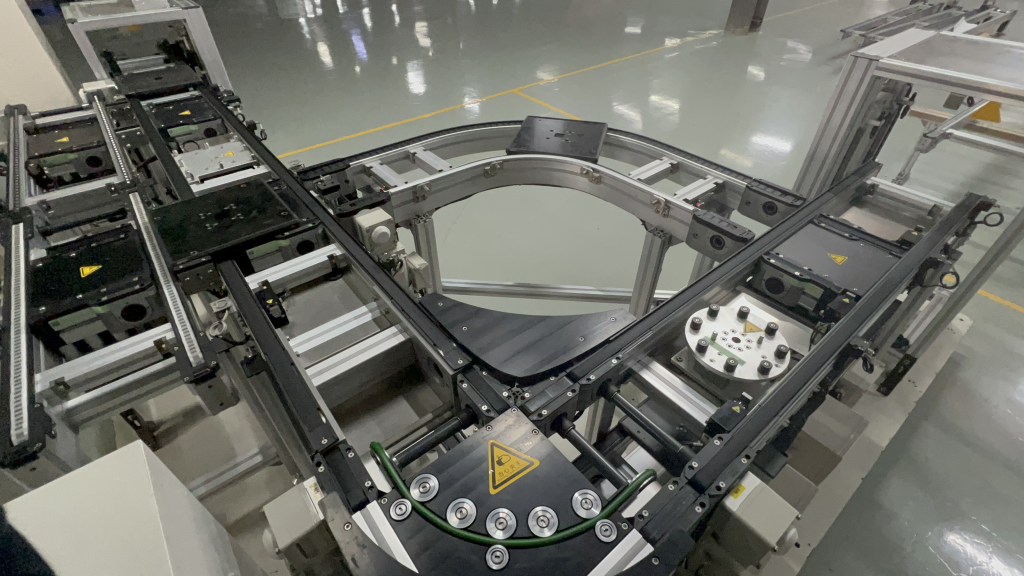
06 Conveyor Layout
Workshop space and line layout are important constraints for selection. Functional components such as turning, lifting and traversing of different conveyor line bodies provide flexible layout solutions. For example, flat-top chain curves support 90° and 180° turns for material flow in complex production lines, while timing belt elevators are suitable for pallet conveying between double- and multi-layer lines to meet the needs of three-dimensional production layouts.
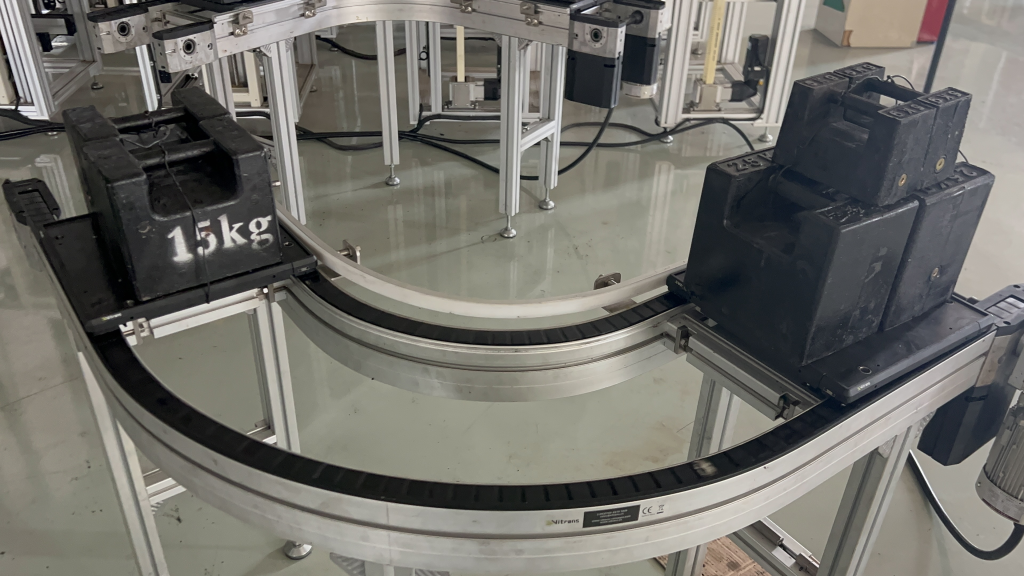
07 Production environment
The temperature, humidity, cleanliness and other factors of the production environment have special requirements for the material and performance of the conveying equipment. For example, in the food processing and pharmaceutical industries, the equipment needs to meet the requirements of moisture-proof, dust-proof and corrosion-proof to ensure the hygiene and safety of the production environment. Wei Chuang's Speed Chain Conveyor Line is made of corrosion-resistant material to adapt to the humid and dusty environment and ensure the long-term stable operation of the equipment.
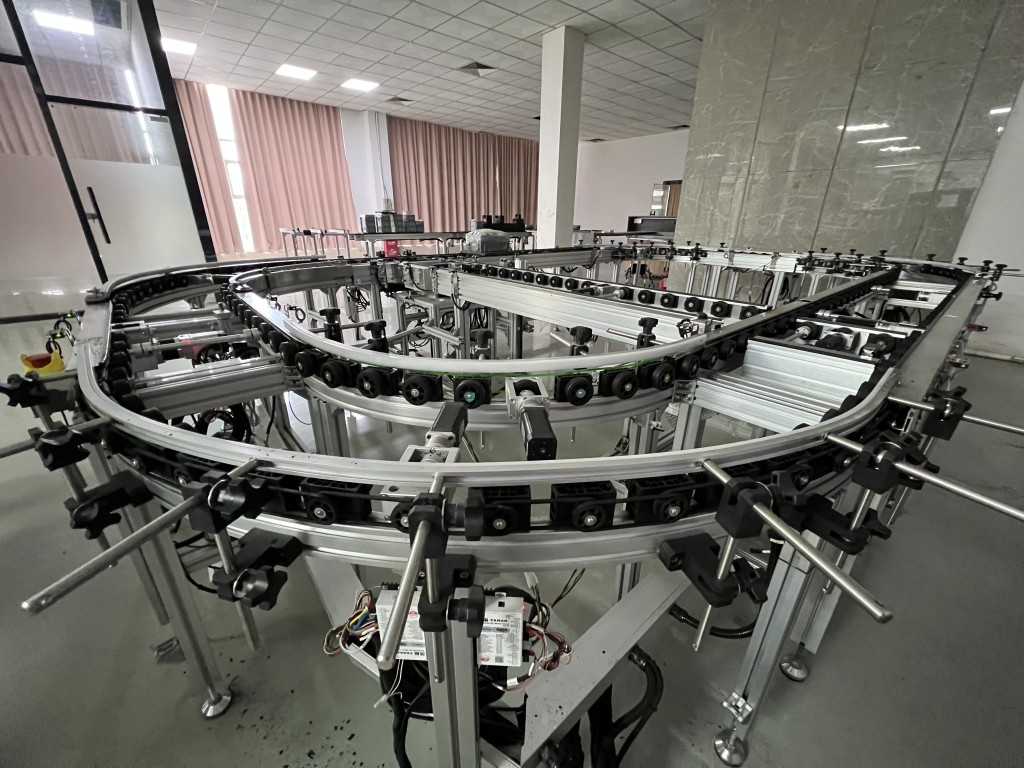
08 Cleanliness requirements
For industries with high cleanliness requirements, such as semiconductors, electronics and pharmaceuticals, conveying equipment needs to be characterised by low dust and no pollution. The cleanliness of overhead chain conveying line can reach over 10,000 levels, and the use of wear-resistant materials reduces the generation of dust, effectively prevents particulate contamination, and ensures the quality of products and the safety of the production environment.
Finally, the key point, when choosing automated conveying equipment, in addition to the quality of the equipment, durability and other equipment itself, in addition to the requirements, to understand the manufacturer's reputation and after-sales service is also very important.
If you are facing the confusion of automation conveyor selection, or want to know more information, welcome to pay attention to Wei Chuang Automation, we will provide you with professional solutions.