In the wave of modern industrial development, production equipment automation upgrade has become an inevitable trend. However, many companies in promoting this process, but generally encountered a "hot under the cold" embarrassing situation: management keen to introduce advanced equipment, the front-line staff are not interested. Behind this phenomenon, what problems are hidden? And how to crack it?
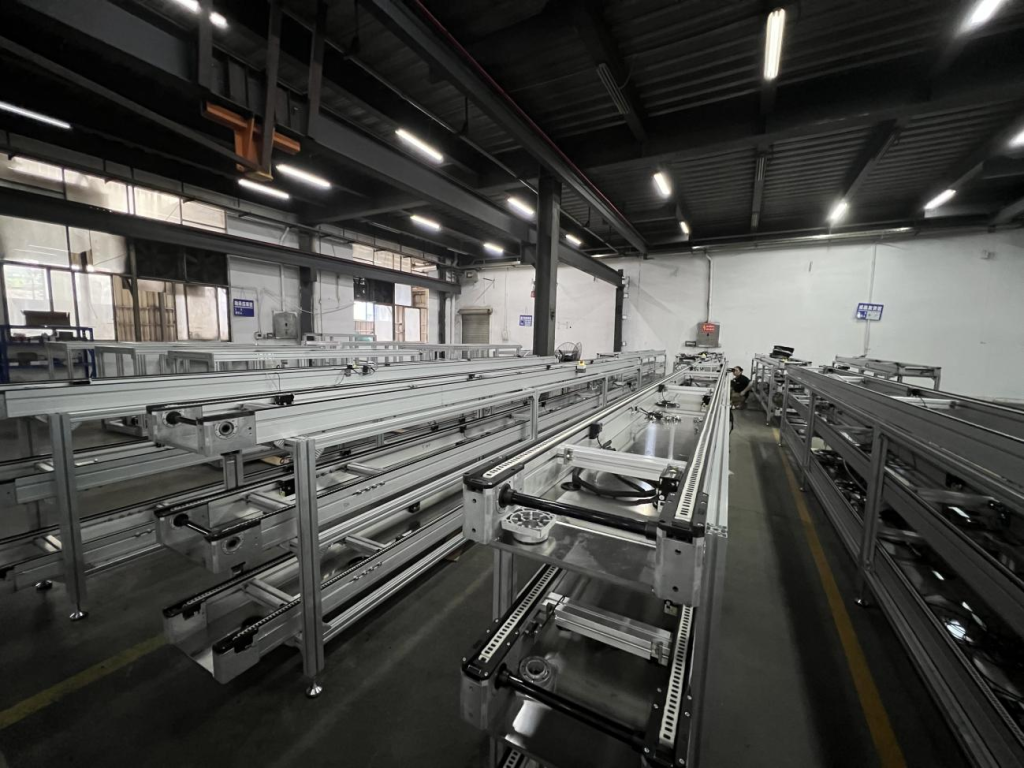
One,corporationsbring inAutomation Equipment Frequently Asked Questions
1,conflict of ideas
The production model of enterprises is mostly characterised by multiple varieties and small batches, which is a natural contradiction to the mass production of single products that automation equipment excels at. Frequent transfer of machines is not only technically difficult and costly to learn, but also a deeper reason for employees to automation equipment may cause unemployment concerns, making them in the early stage of the introduction of equipment to negatively resist, and even question the practicality of automation equipment.
2,Lack of versatility
When introducing automation equipment, some companies lack systematic planning and focus only on immediate production problems, ignoring market changes and future product characteristics. This leads to a lack of versatility and flexibility of the equipment, which can only be adapted to a small number of products. Once the order is reduced, the equipment is idle, waste of resources is inevitable, the enterprise also has concerns about further investment in automation equipment.
3,Evasion of responsibility
The introduction of automation equipment is not a one-day process, and with a limited number of mature solutions on the market, companies often need to communicate with suppliers in depth to customise. However, in the face of the frustration and pressure of this complex process, some of those in charge choose to give up easily and are unwilling to take responsibility, resulting in halfway through the project.
4,Poor system fit
The efficient operation of automation equipment often relies on multi-departmental collaboration. For example, if the production department's scheduling plan fails to match the demand for equipment use, such as splitting the arrangement of products that could have been produced together, it will significantly increase the frequency of machine transfers, further exacerbate employee resistance, and undermine the consistency of automation.
5,Communication and acceptance omissions
Enterprises in the equipment procurement process, if gullible supplier publicity, without adequate communication before the order, and not let the front-line staff to participate in the selection, easy to lead to equipment does not meet the needs. In addition, if the acceptance link is sloppy, not to ensure that employees are skilled in the operation and adjustment of the machine method, the subsequent production problems occur frequently, it is also easy to appear the supplier to assist the possibility of ineffective.
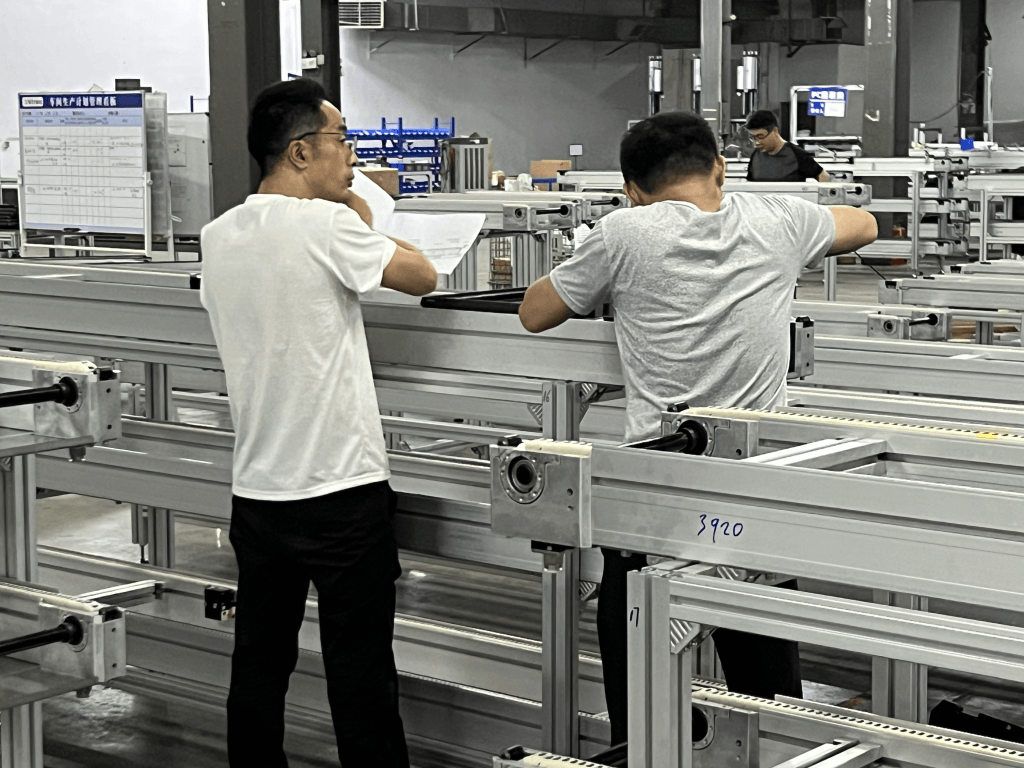
Two,How do I automate the right import?
l Developing a "lazy" mindset
Managers need to change their thinking and proactively look for parts of the production process where machines can do the work for them, or where they can make the work easier for their employees. This "lazy" wisdom is actually a keen eye for automation opportunities.
l be good at borrowing strengths
In the face of resistance to the automation process, whether it is internal coordination problems or external technical bottlenecks, companies should actively leverage the power of leaders, organisational resources, and even external experts to break through the barriers.
l face up to failure
Project failure is not uncommon in automation. The key lies in whether the person in charge can face up to the setbacks with courage and commitment and learn from the experience instead of choking on it. This spirit of trial and error is the driving force behind automation.
l choose wisely
Enterprises need to set automation goals based on their own actual situation, to avoid the blind pursuit of the whole. For small and medium-sized enterprises with limited resources, simple automated or semi-automated equipment may be a more pragmatic choice, because the core value of automation is to save people and energy, rather than the pursuit of high-end.
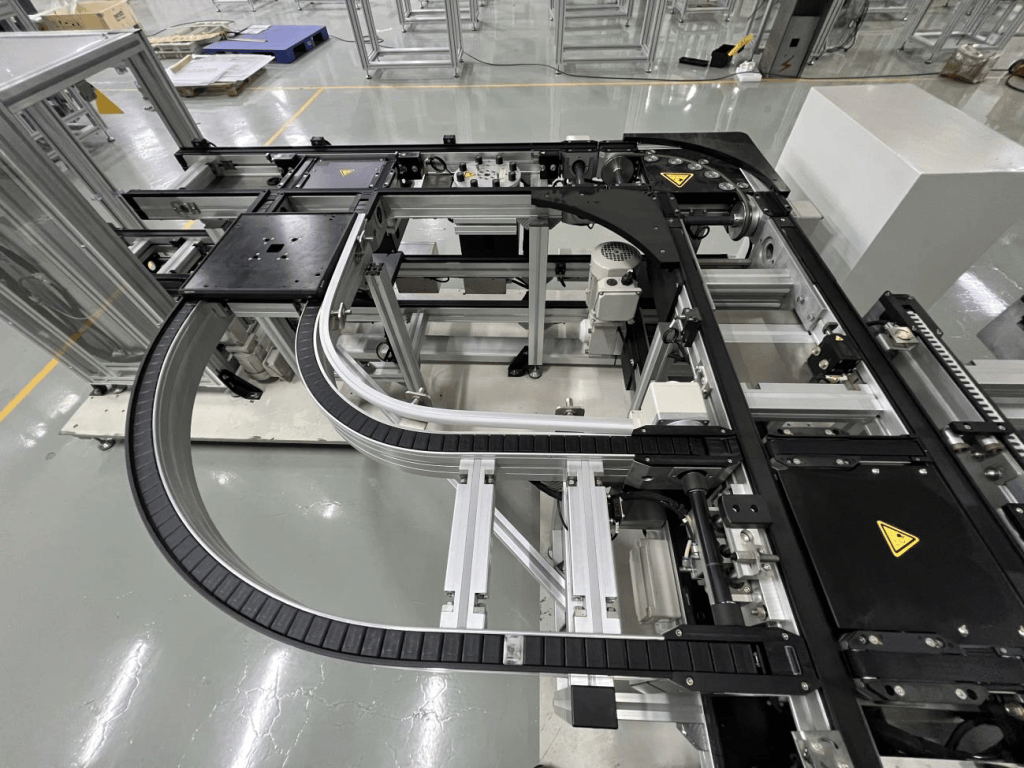
Three,Pinpointing: Identifying Automation Opportunities
Companies should focus on the following jobs and processes to accurately identify opportunity points for automation introduction:
1. Bottleneck processes:Automation can be a powerful tool for breaking bottlenecks in areas where productivity is severely constrained.
2. Cumbersome labour processes:Automation can significantly reduce labour costs for jobs that use a lot of labour and have repetitive and tedious work content.
3. Scrutinising posts:Large batch sizes, small specifications, and high visual inspection requirements, automated inspection can improve accuracy and efficiency.
4. Repeat the lifting manoeuvre:Frequent lifting and carrying movements in the production process are ideal for automation.
5. Error-prone posts:Automation can dramatically improve product consistency and reliability in areas that are prone to human error.
6. Dangerous posts:Automation not only improves efficiency, but also protects the safety of employees in jobs that are dangerous and prone to workplace accidents.
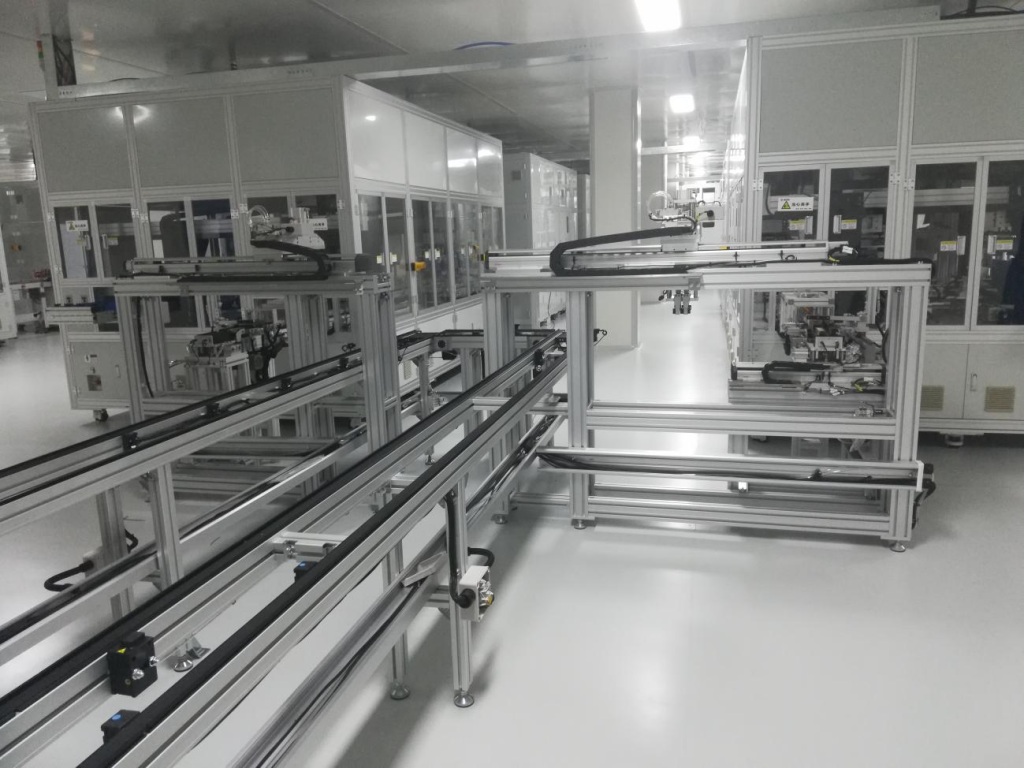
IV. Staff Support - IntroductionThe cornerstone of automation success
Why do organisations often lack employee support when introducing automation equipment?
The root of the problem lies in employees' misgivings about the distribution of benefits brought about by the automation of the enterprise. They are worried about the efficiency improvement, the product processing unit price downward, which in turn affects personal income. Therefore, when promoting automation, enterprises must take the interests of employees into account, and gradually eliminate their concerns. Automation should not be a cold technological replacement, but a deep integration of efficiency and humanity.
The road of automation upgrade is the key for enterprises to move towards efficient and intelligent production. Enterprises can't just automate for the sake of automation, but to import suitable equipment and reach coordinated conditions in order to truly realise the value of automation.