The physical code of the speed-up mechanism: the engineering magic of roller diameter differences
The core mystery of the multiplier chain isDifference in diameter between roller (diameter D) and roller (diameter d). When the chain is running at speed V₁, the actual speed of the work plate can be as high asV₁×(1+D/d)This is the first time that the production line has been designed to achieve a 2-3 times increase in speed. This seemingly simple mechanical design actually reconfigures the time-space relationship on the production line:
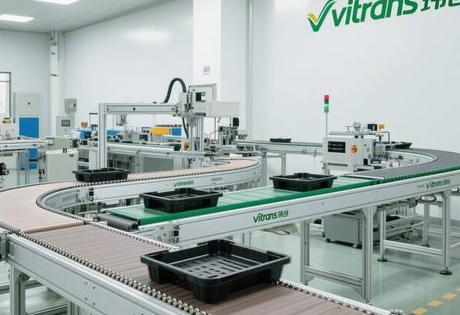
- Dynamic accumulation controlThe workpiece plate is accurately suspended by the blocker (error ≤±0.5mm) and automatically flows after operation, forming a flexible beat of "continuous conveying + fixed-point operation";
- Triple structure evolution::
- jacketed(low cost and easy to manufacture)
- inserted(Early commercial mainstream)
- inlaid(Optimal resistance to deformation under heavy load);
- Extreme Environment AdaptationAlloy steel chain with 600℃ resistance solves the conveying problem in heat treatment workshop, while self-lubricating coating overcomes the maintenance pain point in dusty environment.
personal insight: The essence of the multiplier chain isReplacing electronic controls with mechanical intelligence-- "Passive intelligence" through physical structures, which explains its penetration rate of up to 68% in small and medium-sized manufacturing enterprises (China Intelligent Manufacturing White Paper, 2024). Compared to systems relying on complex algorithms, the reliability of mechanical incremental speed is irreplaceable in stability-sensitive scenarios.
![]()
The technological divide between the four types of multiplier chains: from immediate needs to higher-order evolution
I. Fixed multiplier chains: a universal choice that prioritises economy
- Speed characteristics: Constant 2-3 times speed increase (chain 1m/s → workpiece 3m/s)
- cutting edgeFailure rate <0.5 times/thousand hours, suitable for standardised production lines such as microwave oven assembly.
- restrict sth. within set boundaries: Beat curing, unable to respond to flexible demands
Second, double speed multiplier chain: precision and efficiency of the balancing act
- dual mode collaboration::
- Low-speed section (0.5-1m/s): Precision Headlight Lens Installation
- High-speed section (2-3 m/s): Quick transfer across work stations;
- Spatial innovation: a car company throughTop lift transplanter articulated two-speed zone, site utilisation increased by 40%.
III. Variable Speed Chain: The Ultimate Form of Flexible Manufacturing
- technological breakthrough: servo motors + tilting guides to realise1-4 times infinitely variable speed
- Data Enablement: Suzhou electronics factory access to MES dynamically adjusted speed, peak capacity increased 22%
- Cost constraints: Higher cost of 300% than fixed chain, payback period >3 years
IV. Accumulated multiplier chains: the pinnacle of the art of cushioning
- core value: The chain continues to run when the workpiece is suspended, eliminating the traditional "start-stop loss" of the line body.
- Performance Cases: Inspection station with 4 stacking positions, improving the efficiency of traceability of good products by 35%.
Technology Convergence in the Automotive and Electronics Industries: Scenario-Based Innovation Fact Sheet
New energy battery PACK line (Ningde Times model)
- Magnetic Levitation Vibration Resistant Tray: Core transport vibration <0.1G (national standard 1G)
- Static dissipative chainStatic voltage control <50V, avoid PCB breakdown
- efficacy: Cell damage rate reduced from 0.07% to 0.002%
High-end lamp assembly line (Bosch Suzhou Plant)
- Dual Speed Chain + Visual Positioning::
- 0.8m/s precision mounted optical lens
- 3m/s to complete the aging test;
- Data Assetisation: 2.7TB of process parameters are generated annually for a single tooling board, driving dynamic optimisation of recipes.
Subversive revelations: The doubler chain has evolved from a conveyor to aData Acquisition Terminal-- Its value is not only in handling materials, but also as a real-time sensor of the production process.
The Intelligent Leap of Speed Chain: Breaking the Three Technical Shackles
Precision Components Vibration Resistance Challenges
- sore point: Chip solder joint breakage rate rises sharply at acceleration > 0.5G.
- (of ball sports) break through a defense: Carbon Fibre-Nylon Composite Work Plate Vibration Damping 42%
The spell of the long line break
- risk point: >40 metres of wire body single-segment stress concentration leading to rupture cycle <2 years
- programme: 12m segmented module + intelligent tensioning system (tension fluctuation <5%)
Multi-species mixed-flow scheduling hysteresis
- conflicting views: Traditional PLC model switchover response latency of 12 seconds vs. 1 minute required on the production line.
- collapse (of plan, talks etc): Edge computing nodes enable 500ms-level policy switching
Forward-looking layout: "intelligent ambush" for the future
Hardware Reservation Strategy::
- Pre-set T-slots on both sides of the guideway for quick retrofitting of photoelectric sensors (e.g. Omron series);
- Power channel redundancy design to avoid flying wires for later modifications.
open software architecture::
- Select a PLC that supports Profinet, EtherCAT protocols (e.g. Siemens S7-1200);
- Touch screen reserved script interface (Wyland MT8102iE) to support dynamic adjustment of process parameters.
Load and space redundancy::
- When the current load is 500kg, select the motor according to 800kg;
- A 3-5 metre extension area is reserved at both ends of the line to cope with additional workstations.
Exclusive data prognosis::
The focus of competition for speed chains will shift from "mechanical growth rates" to "mechanical growth rates" in 2026."Data Carrying Capacity"-Can real-time process 10,000 workpiece board state streams per second will be the watershed in distinguishing equipment from intelligent systems. Initial investment in adding 10%-15% for forward-looking design can reduce future 30% retrofit costs.
Readers' core questions answered
Q1: Why is a doubler chain more suitable for automotive assembly than a belt line?
A1: The core differences areFunctional positioning and physical limits::
- doubled speed chain: ±0.5mm precise positioning, 4000kg heavy-duty capacity, dynamic accumulation - perfect match for the assembly of heavy parts such as engine blocks;
- leather belt line: Light load (20m/s) - only for scenarios such as courier sorting.
Q2: How to solve the problem of prohibited lubricants for food lines?
A2: Intrinsic countermeasures for lubricant contamination risks:
- Material innovation: Food grade POM self-lubricating chain (coefficient of friction 0.15-0.2);
- Surface technology: Ceramic coated rollers (life > 50,000 hours).
Q3: Does the smart retrofit require a full replacement?
A3: A three-stage gradual path to low-cost upgrading:
- IoT: Installation of vibration sensors (<¥80,000) to monitor chain health in real time;
- digitisation: Deploy edge gateways (¥150-300k) for workstation data binding;
- intellectualise: AI Dynamic Beat System (ROI > 40%) optimises energy efficiency across the board.
industry corroboration: After the phased transformation of Jiu Mu Sanitary Ware, the multiplier chain downtime decreased by 73%, verifying thatThe Economics of Progressive Smart Transformation.