I. Technology Kernel: The Physical Code of Geometric Growth Rate
of a multiplier chainCore Mysterylies in its unique two-stage motion system. When the inner chain roller (diameter d) runs at the base speed V₁, the outer chain roller (diameter D) triggers an additional linear velocity V₂ = (D/d) x V₁ under the pressure of the workpiece plate, culminating in aTotal V = V₁ x (1 + D/d)The multiplier effect. For example, when D=2d, the speed of the work plate can be up to 3 times the speed of the chain, realising the wonder of "low-speed chain, high-speed conveying".
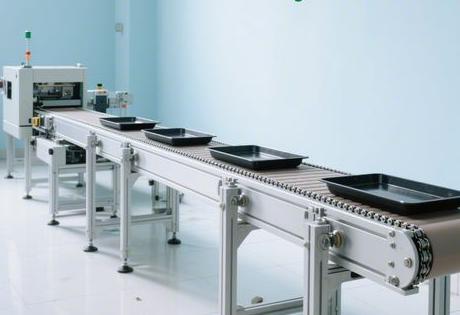
This design shows revolutionary value in industrial scenarios:
- Dynamic shifting capability: Through the linkage of laser sensor and pneumatic stopper, the workpiece plate is conveyed at a high speed of 18m/min in the no-load section, and then the speed is accurately reduced to 2m/min with an error of ≤0.5mm when entering the assembly area;
- energy consumption subversionRolling friction replaces traditional sliding friction, reducing energy consumption by 40% and avoiding vibration damage to electronic components;
- Extreme environmental toleranceSpecial alloy steel chain has a life span of 3 years in 85% humidity and 50℃ environment, which is 400% higher than ordinary chain.
II. System upgrade: from mechanical transmission to intelligent decision-making centre
Modern speed chains have evolved beyond the realm of mere conveyors intoNeural Networks for Factories. Companies such as Weitron Automation are making this leap through three major innovations:
▋ Hardware modularity revolution
- Bearing innovation: Engineering plastic rollers (2200kg for light loads) and steel rollers (4000kg for heavy loads) are configured as required to spread the pressure by increasing the contact surface;
- anti-interference design: Closed guide rail + self-cleaning roller structure compresses the dust channel to ≤2mm, completely solving the risk of jamming;
- distributed driverThe 600m line body is divided into 12 independent drive sections, and the jacking and shifting mechanism automatically diverts the flow in case of a single point of failure, reducing downtime losses by 87%.
▋ Intelligent penetration of control systems
- Dynamic Beat Adjustment: PLC programming real-time adjustment of blocking timing, the same production line mixed production of high-end products (station stop 120 seconds) and basic models (stop 60 seconds), switching time tends to be close to zero;
- digital twin prediction: Workpiece panels embedded with RFID chips, synchronised mapping of kiln temperature profiles, air tightness data, and early warning of equipment failure 14 days in advance.
When the physical speed increase mechanism is deeply integrated with the data flow, the essence of the speed doubling chain has been transformed from a "conveying tool" to a "decision-making hub" - the diameter of the rollers. The 13% efficiency improvement brought by every 0.1mm increase is actually a quantum leap in the decision-making precision of the entire manufacturing system.
III. Industry Empowerment: Practical Solutions to Crack the Pain Points of Smart Manufacturing
▋ Automotive manufacturing: a model for heavy-duty precision assembly
In the electric vehicle chassis production line, the doubling chain carries 500kg battery packs to completion:
- millimetre positioning: ±0.5mm repeatable positioning accuracy, so that the wiring harness plugging pass rate jumped to 99.6%;
- High-temperature battlefield breakthrough: Resistant to 120°C coating chain for continuous operation and heat radiation from the battery pack gluing process.
▋ Electronic Semiconductors: Micron Clean Conveying
In the chip packaging workshop, the triple purification design overturns the tradition:
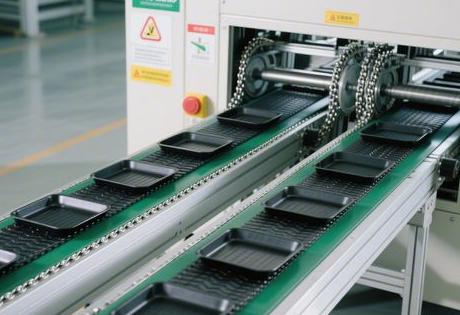
- Static elimination roller: Eliminate particle adsorption;
- Oil-free bearings: Eliminate lubrication contamination;
- Enclosed rails: Isolation of external dust.
Achievement of ISO Class 3 cleanliness standard and 67% reduction in defect rate.
▋ New energy batteries: a new paradigm for energy efficiency balance
Innovative practices in the Ningde Times factory:
- Gravitational potential energy recovery: Falling section power generation technology with auxiliary power supply self-sufficiency of 18%;
- Carbon Fibre Workplace Panel: Reduced weight 30% reduces chain load and saves 240,000 kWh per year on a single line.
IV. Technical challenges and ways to break the ice
Despite the significant advantages, the multiplier chain still faces two core contradictions:
Contradiction 1: The game of non-standard customisation and cost control
sore point: Differences in plant heights and process rhythms among SMEs lead to high retrofitting costs.
collapse (of plan, talks etc)::
- Modular Architecture: 250-900mm width-adjustable aluminium profile base frame + 750W inverter motor power module, supporting free combination of plane/vertical layout;
- Rental Sharing ModelFlywheel and other enterprises to launch "pay per metre" service, the initial investment compressed to the traditional programme 20%.
Paradox 2: Balancing energy efficiency and longevity
sore point: High-temperature environment accelerates chain wear, with monthly wear rate exceeding 0.1mm.
collapse (of plan, talks etc)::
- Microporous oil penetration technology: Formation of an oil film protection layer inside the guideway, reducing the wear rate to 0.03mm/month in a 50°C environment and extending the life of the guideway by 400%;
- Photovoltaic Direct Supply SystemWujiang factory roof solar panels for the speed chain power supply accounted for 41%, breaking the "high energy-consuming automation" curse.
V. A picture of the future: the nerve centre of an ultra-flexible manufacturing system
Multiplier chain technology is undergoing three major paradigm leaps:
- human-computer collaboration reconfigurationWhen workers wear AR glasses to receive instructions, the robotic arm delivers tools and materials synchronously, and the assembly efficiency of the Bosch Suzhou plant has increased by 40% and the error rate has gone to zero;
- Code-free flexible configurationThe prototype of the Bowie and 2024 supports the switching of up to three product models per hour on the production line: a drag-and-drop interface to reorganise the workstation process;
- The bio-based materials revolution: Biodegradable chain oil reduces hazardous waste emissions by 3 tonnes per annum and reduces carbon footprint by 621 TP3T.
Ask Yourself: In-depth Analysis of Technical Concerns
▋ Why is the work plate speed often limited to 15m/min?
Dynamic balance of safety and precision: Inertial displacement exceeds 2mm at >15m/min, affecting precision assembly. But bySegmented speed control strategy(18m/min in the non-operating area → 2m/min in the assembly area), the combined efficiency is still 3 times that of the conventional line.
▋ How to prevent jamming in ceramic dusty environments?
Self-cleaning rollers + closed guidesDouble insurance: dust channel ≤ 2mm design, Jiu Mu Nanan factory 100,000 times cycle test zero failure.
▋ Do I have to customise the whole line?
Modular combination to solve the dilemma: the basic framework (accounting for 60% of the cost) is standardised, and only 30% components need to be customised according to the working conditions. Measurement of Wei Chuang Automation shows that this mode shortens the delivery cycle to 45 days.
▋ Can it be compatible with old production lines?
grafting-inHas become a trend: a home appliance enterprises to retain the original drum line main body, only to replace the drive section for the speed chain module, after the transformation of the efficiency to enhance 200%, the payback period <8 months.