As an indispensable part of modern automated production lines, pallet conveyor lines play a key role in material handling and flow. However, because of the different plant layouts, production line configurations and the diversity of product characteristics, the pallet conveyor line often needs to be personalised according to the actual needs. How to realise the high efficiency and intelligence of the production line?
Here are a few points about customisationPallet conveying lineDetails and requirements that should be attended to:
One,Load and pallet specifications
01load capacity
definePallet conveying lineWhen considering the load capacity of a conveyor line, it is necessary to take into account the weight of the product, the weight of the workpiece and the weight of the bottom bracket, and choose the appropriate type of conveyor line, such as roller conveyor line or speed chain conveyor line.
02Pallet size
According to product specifications, workpiece design and the size limitations of special mechanisms of the conveyor line (e.g. turns, elevators), the appropriate pallet size is selected to ensure interchangeability and versatility.
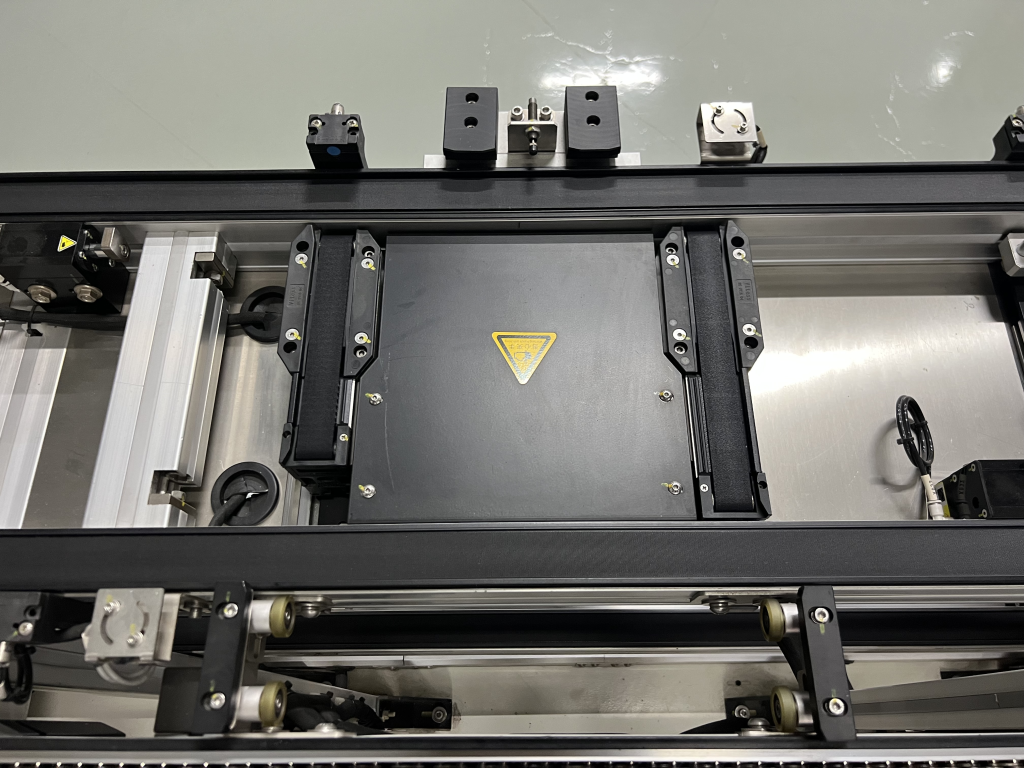
Second, the length and layout of the conveyor line
01length plan
- Through on-site measurement to determine the starting point, end point and key node location, combined with the material conveying speed, beat requirements, calculate the required length of the conveying line.
- Consider special terrain such as turns and climbs to ensure smooth running of the conveyor line.
02Layout optimisation
- Optimisation of conveyor paths to reduce unnecessary conveyor distances and waiting times.
- Use modular design to achieve flexible combination and expansion to adapt to future layout changes.
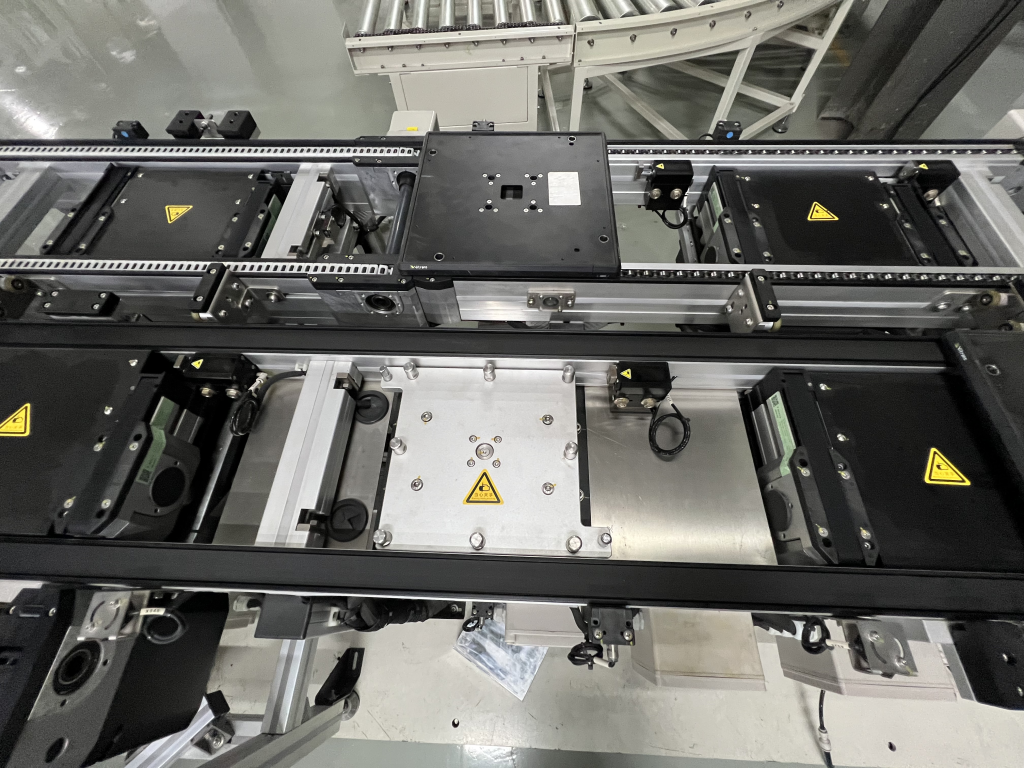
Three,Height setting and ease of operation
01Height setting
- The height should be set taking into account the ease of material handling, operator height and conveyor line stability.
- Ensure that the conveying line is at the same height as the upstream and downstream equipment docking, and that the material flow is smooth.
02Ease of operation
- Installation of additional auxiliary facilities such as operating platforms, handrails and lighting fixtures.
- Through intelligent control to achieve automatic start-stop, speed adjustment and fault alarm, reduce the intensity of operation.
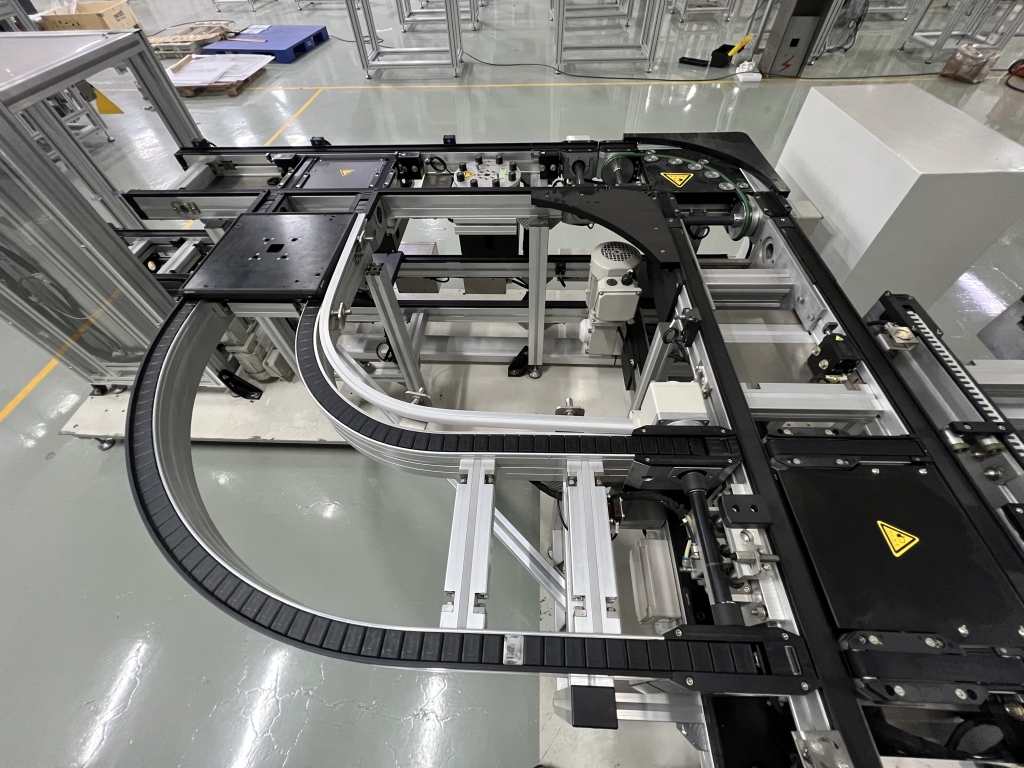
IV. Selection of key components
01Media Type
According to the characteristics of materials, conveying environment and load requirements, select theTiming belts, flat belts, stacked roller chainsmaybePlastic overhead chainand other conveying media.
02Material Selection
Choose the architecture material, such as steel, stainless steel or aluminium profile, according to the material weight, conveying speed and workshop environment.
03Functionality Expansion
- Additional functions such as stoppers, jacking positioning units, etc. are added on request.
- In special environments (e.g. high temperature, humidity), install appropriate protective measures.
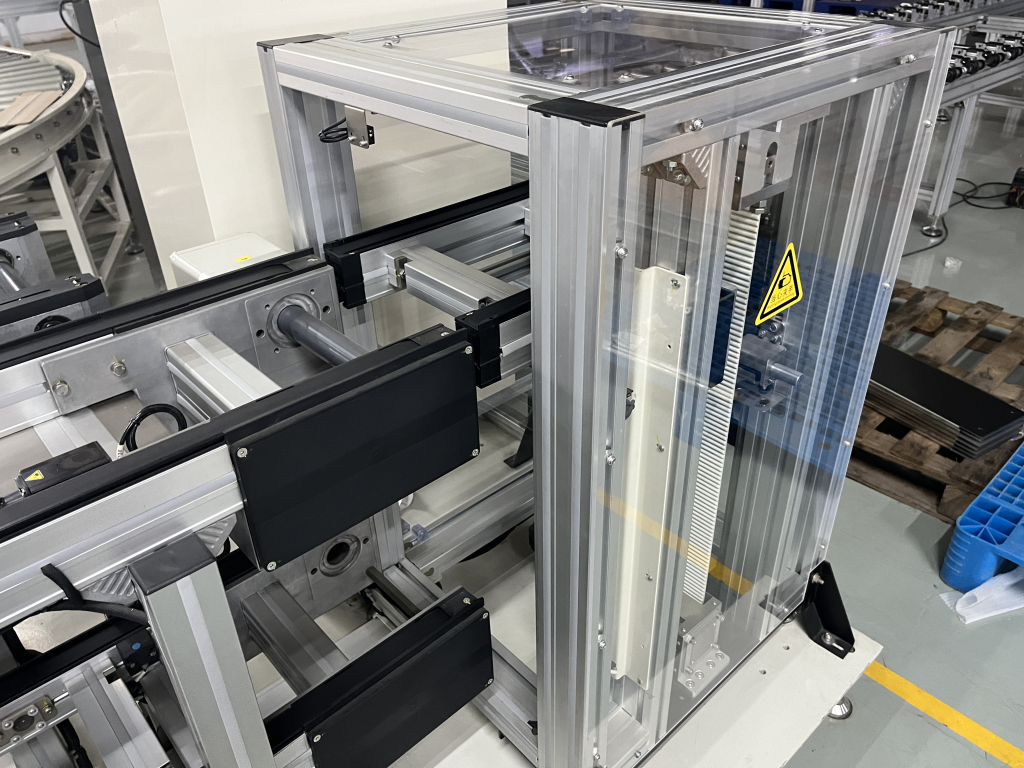
5Key implementation points
01Parameter clarity
Precise data on size/load/speed etc. is required.
02Supplier Selection
Choose manufacturers with rich industry cases and technical strength to ensure product quality and after-sales service.
03acceptance test
Positioning calibration and load continuous operation tests are required.
04Personnel training
Train operators in key operations such as start-stop, emergency stop, and fault reset.
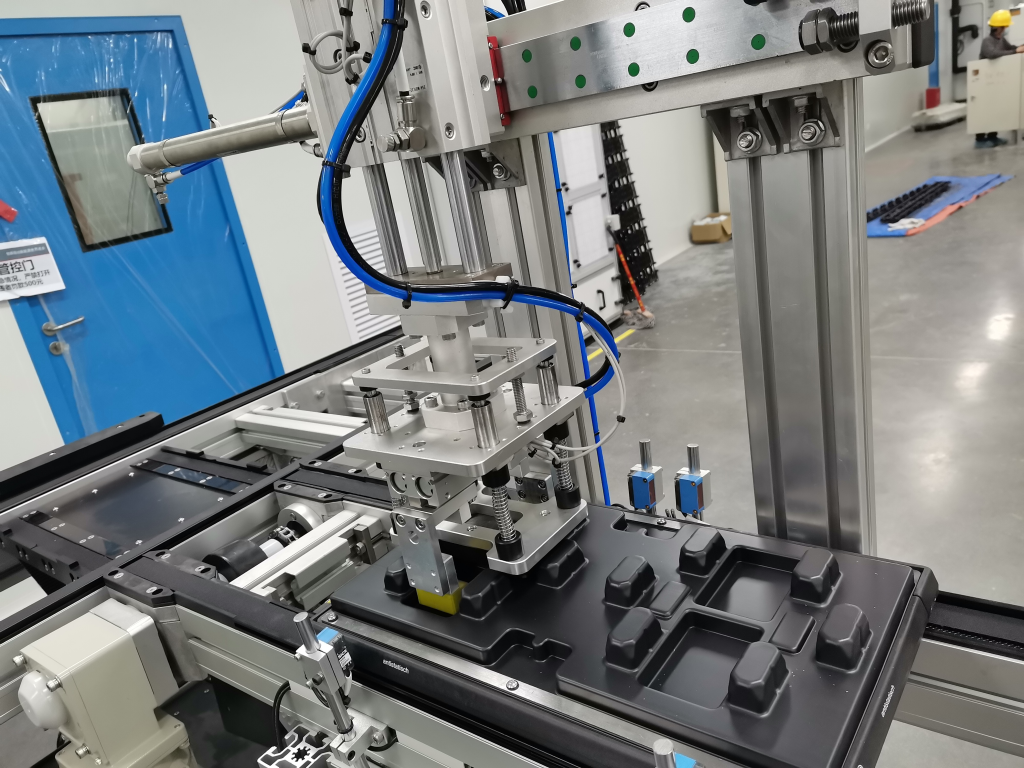