Core purchasing dimensions: technology suitability and vendor capabilities
Space Folding Designis the core value of the double-layer multiplier chain, which, through theUpper assembly layer + lower return layerThe vertical architecture, to achieve synchronous operation of material handling and workpiece board cycle, space utilisation is improved by 60%. Selection needs to be focused on:
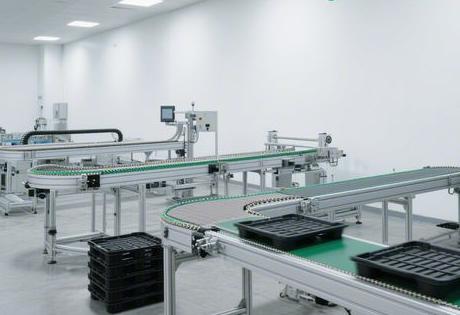
- Material ProcessThe guide rail should be made of 118×100mm high-strength aluminium profile (bending strength ≥180MPa), and the chain should support triple-speed engineering plastic chain to avoid rusting of carbon steel in the humid environment;
- load capacityHeavy load scenarios (e.g. engine assembly) need to be equipped with steel roller chains (allowable load 5.88kN-m), while light load areas can be equipped with engineering plastic chains to reduce weight and noise;
- synchronised control: Preferred single-motor coaxial drive solution, physical elimination of speed deviation, split drive requires PLC dynamic speed regulation (response time <10ms).
personal experienceThe current manufacturers often advertise "all stainless steel chain", in fact, local reinforcement is better - pharmaceutical line only in the filling area using titanium alloy coated chain plate, other areas with carbon steel + ceramic coating, the cost of 45% and the life of the same. Life expectancy is the same. Blindly stacking materials to cost redundancy.
Supplier panorama analysis: from source factories to regional service providers
1. Yangtze River Delta cluster: leading in technology and speed of delivery
- Changzhou Guangliang Intelligent: 2700㎡ production base, support 7-15 days shipment, base module stocking rate of 70%, cost lower than peers 10% (aluminium profile rail reuse rate of more than 60%);
- Suzhou Weitop: The magnetic levitation drive solution is energy efficient 40%, which is suitable for the new 2026 energy efficiency standard, but the customisation period is long (about 25 days).
2. Pearl River Delta Innovation Network: Intelligence and Industry Solutions
- Shenzhen Yinzhuo Industry: Focus on 3C electronics, RFID link routing technology to shorten the mixing line switching time by 73%, and the positioning accuracy of the workpiece board ±0.1mm;
- Dongguan Jialian Automation: The digital twin O&M system predicts failures and improves OEE to 921 TP3T, but the price is 151 TP3T higher than the industry average.
3. Northern Service Hub: heavy load and localised response
- Tianjin Guanrui IndustryCustomised six-axis levelling jacking mechanism for new energy vehicle battery packs (load capacity 280kg±0.05°), with defective rate reduced from 1.2% to 0.3%;
- Hefei Jieming Electromechanical12-hour on-site maintenance in the province, suitable for pharmaceutical aseptic lines and other scenarios with "zero tolerance" for downtime.
Customisation Process Explained: Avoiding the Four Pitfalls
1. Requirements definition phase (30% of cycle time)
- scene couplingNew energy vehicle battery assembly needs to be embedded with membrane pressure sensors (sampling frequency 1kHz), and pharmaceutical aseptic lines need independent negative pressure air ducts (microbiological control <1CFU/m³);
- parameter trap: Additional support structure is required when the width of the wire body is >900mm, and blind widening may cause the deformation rate to rise 30%.
2. Modular cost reduction strategy
- Foundation module (60% cost): Mitsubishi PLC control unit, standard aluminium profile rail scale reuse;
- Industry Kits (40% cost): Silicon nitride ceramic rollers for semiconductors (particle shedding rate <0.01%), titanium alloy coated chain plates for food lines (salt spray resistance ↑300%).
3. Quantification of acceptance criteria
markdownmake a copy ofCommissioning cycle ≤ 28 days (industry average 45 days) Failure response: 12h in the province / 24h outside the province to the scene [1](@ref) Warranty terms: 1 year free warranty + lifetime maintenance (need to specify the list of wearing parts)
Balancing cost and value: full lifecycle ROI
- initial investment: The custom line is 30% higher than the standard line, but the modular design reduces the cost of later modifications;
- O&M costs: The inclusion of PTFE grease extends maintenance intervals to 3 months, saving one power plant $470,000 per year;
- loss on failure: Intelligent Early Warning System has suppressed average annual downtime from 86 hours to 7 hours, with a capacity utilisation of 921 TP3T.
Hidden Cost Alert::
2.9 million in damages to a factory that crashed its guide rails because it did not have a hard limit on cylinder travel.Mechanical + electrical double insuranceIt's the bottom line of safety. Physical blocks cost only 0.31 TP3T of the total equipment price, yet reduce failure rates by 501 TP3T.
Exclusive Sourcing Strategies: A Three-Stage Decision Model
- short term needs(<20 days delivery):
- optionChangzhou Guangliangand other vendors with basic module inventories, parallel engineering to compress the critical path;
- technical assault(High Precision/Clean Scene)
- Semiconductor Line SelectionShenzhen Yinzhuo(antistatic chain 10⁶-10⁹Ω), medical line selectionTianjin Guanrui(Class A laminar flow ± 0.5°C);
- Long-term cooperation::
- agree to and sign (a treaty etc)ladder price agreement: 3% discount for purchasing more than 500 metres per year, locking in the risk of raw material fluctuations.
Ask Yourself: Three Questions for Procurement Decisions
Q: How can I verify the vendor's true delivery capability?
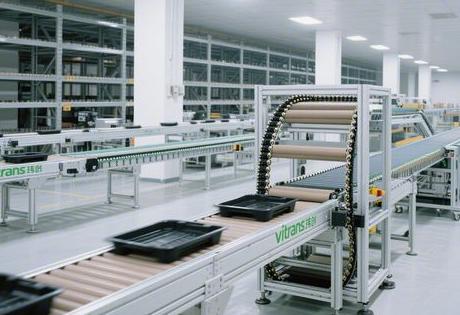
Answer.Four-step factory inspection method::
- Unannounced visits to production sites: check aluminium profile stock levels (≥1000m as a safety line);
- Request acceptance reports for cases such as the Tennant Group;
- Stress testing: Requirement to produce a sketch of a customised solution within 72 hours;
- Verify maintenance team density (e.g. ≥ 5 engineers per province).
Q: Do low bids hide risks?
Answer.Cost Breakdown Comparison: If the offer is below the industry average of 15%, be wary:
- Whether to replace the 118 x 100 rail with 40 x 40 aluminium (bending strength ↓60%);
- Whether to omit the digital twin pre-validation session (mechanical shock risk ↑50%).
Q: How to avoid equipment "not suitable for the soil"?
Answer.Tripartite Joint Coordination Mechanism::
- SolidWorks Motion simulation report from the vendor;
- Third party organisations do on-site FAT (Factory Acceptance Testing);
- Corporate electricians are involved in grounding resistance calibration (≥10⁶Ω required for anti-static).
data pivot: In 2025, the head manufacturer's capacity reaches 12,000 metres/year, but the actual delivery is only 7,800 metres - choosing a manufacturer with a capacity utilisation rate of 65%-80% can safeguard the pace of delivery while avoiding QC slippage due to capacity overload.