Bi-level system-specific jamming: a source of upper and lower level conflict
The problem of lagging in double-layer multiplier chains often arises from theSeverance of upper and lower structures or operations, needs to be targeted and cracked:
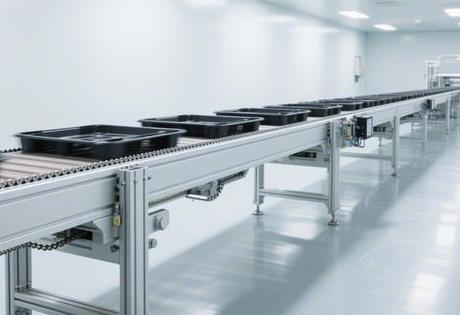
- The structural difference trap: Mismatch between upper and lower chain pitch, guide rail inclination or load capacity (e.g. upper light load chain pitch 25.4mm, lower heavy load chain 38.1mm), resulting in misalignment of engagement or sudden increase in friction resistance.
- operational asynchrony crisisWhen the split motor is driven, the speed deviation of the upper and lower layers is >5%, which triggers the collision of the workpiece boards or the blockage of the return flow. In the case of an automobile factory, the high-frequency starting and stopping of the upper sorting section and the even-speed return of the lower layer led to the accumulation of 23% of trays at the articulation.
- functional logic conflict: The upper level needs to be sorted quickly (speed 1.5m/s), the lower level needs to be cached (0.3m/s), and the PLC instruction conflict triggers an emergency stop when the control programme is not partitioned and designed.
The deep-rooted causes of mechanical lag and precise response
1. Failure of the chain system
- Wear and tear chain reaction::
- Link elongation overrun (>2% wheelbase) causes engagement failure and elevated risk of jamming 300%.
- Roller bias grinding triggered by lateral force surge, guideway local extrusion deformation > 0.5mm is stuck.
- prescription::
- replacementsWear-resistant alloy sprocket(tooth face hardening HRC60+) andUniform upper and lower pitch.
- mountingAutomatic Cleaning Brush + Magnetic AttachmentIntercepts metal debris (99% for debris with particle size >1mm).
2. The deadly game of rails and loads
- design flaw::
- Bend radius <10 times chain pitch (e.g. bend R <381mm for pitch 38.1mm), centrifugal force causes rollers to squeeze the side wall of the guide rail.
- When the centre of gravity of the workpiece plate is offset >50mm, the roller is overloaded with 200% pressure on one side, accelerating the jamming.
- Innovative adjustments::
- optimisationGuideway tilt angle(3°-5° recommended) and increase the number ofPolyurethane support wheelThe coefficient of friction is reduced to 0.05.
- adoptionLoad cell + AI balancing algorithm, real-time warning centre of gravity shift.
A simultaneous revolution in electricity and control
1. Driver system upgrades
- Synchronisation::
- Replace the split motor withSingle motor + double output reducer, eliminating speed differentials (651 TP3T reduction in failure rate after a plant modification).
- riseEncoder feedback closed loopThe speed control accuracy is up to ±0.1m/s.
- Energy optimisation::
- Frequency inverter + braking resistorCombination to address start-stop oscillations (acceleration time extended to 5 seconds, overcurrent risk reduced to 80%).
2. Intelligent diagnostic system
- Three-layer defence mechanism::
- Real-time monitoring layer: Vibration sensors capture >5kHz anomaly spectrum to warn of bearing wear (2 weeks in advance).
- Dynamic tuning layer: RFID commands to triage job boards and reduce manual intervention 30%.
- digital twin: 3D model simulates thermal expansion (2.3 mm/m expansion/contraction at 30°C difference in temperature) and pre-adjustment of the tensioning force.
Customised solutions for industries
- Electronic assembly line::
- Anti-static work plate + ±0.5mm pneumatic stopper to eliminate patch offset jamming.
- Engineered plastic chain noise reduction to <60dB to avoid vibration interference with the sensor.
- Automotive Heavy Duty Line::
- Hydraulic buffer absorbs 70% impact kinetic energy, and carbon steel chain carries 800kg to prevent deformation and jamming.
- Food Aseptic Line::
- CIP cleaning nozzles prevent grease build-up and self-lubricating ceramic bearings are maintenance-free.
Reconfiguring maintenance strategy: from reactive repair to proactive prevention
- (soup etc) of the day::
- Check the state of chain lubrication (replenish oil immediately if the dry friction coefficient is >0.01).
- Test emergency stop button response (≤ 0.2 seconds).
- every month::
- Calibration sensor (photoelectric eye deviation ≤ 1mm).
- Hydraulic tensioning device to adjust the sag (standard ≤ 2cm).
- annual overhaul::
- Replace the high temperature resistant grease (e.g. Shell Gadus S2 V220) and clean the old oil.
personal viewpoint: Currently, 90% enterprises still adopt the "post-failure maintenance" model, which is actuallyEvery $1 of preventive input avoids $8 of lost production... A 3C plant compresses stuck downtime to 4 minutes/month with AI predictive maintenance -Data-driven predictive maintenance is the ultimate weapon to break jams.
Ask Yourself: Three Questions to Tackle Jams
Q: What is the permissible speed difference between the upper and lower levels?
A: The safety threshold is≤3%.. If the upper layer has a speed of 1.0m/s, the lower layer needs to be kept at 0.97-1.03m/s, which can be achieved by theCoaxial drives or PLC synchronisation modulesRealisation.
Q: Priority of emergency treatment for jams?
A: The Golden Three Steps:![]()
- Immediate shutdown: Trigger the emergency stop button to prevent secondary damage;
- locate a choke point: Check for foreign objects (30% jams originating from metal shavings), chain slack, and sensor condition;
- segmentation test: Isolate problem segments to avoid total paralysis.
Q: Retrofit payback cycle?
A: an automobile factory data: invested ¥ 800,000 to upgrade the intelligent synchronisation system (accounting for the cost of line body 18%), reducing the failure rate of 65%, save ¥ 2.2 million in annual losses of production stoppages.Recovery cycle <5 months.
Exclusive data:: Industry report 2025 shows a two-tier multiplier chain with synchronous optimisation + predictive maintenance.Decrease in jamming frequency 82%The magnetic levitation technology (Suzhou laboratory has landed) will further eliminate physical friction jams - when the manufacturing industry from "passive response" to "active immunity! When the manufacturing industry shifts from "passive response" to "active immunity", the production line toughness revolution will really come.