一、核心技术原理:空间与效率的协同进化
双层顶升倍速链的精髓在于“垂直空间复用”与“动态分流” 的融合设计。其核心运行逻辑包含三层机制:

- 差速传动:通过工装板底部滚轮直径(D)与链条滚子直径(d)的比值实现增速,工装板实际速度=链条速度×(1+D/d),典型应用可达2-3倍增速
- jacking and translating:移载机在上下层衔接处完成关键动作——液压或气动顶升机构将空载板抬离上层轨道,平移机构横向转移至下层回流线起始端
- 智能阻停:各工位配置光电传感器与阻挡气缸联动,响应时间≤0.5秒,实现工装板毫米级精准停位
宁波凯风2024年专利揭示的缓冲挡块设计解决了行业痛点:在空载板下落时,聚氨酯缓冲模块吸收60%冲击能量,配合滑块-滑轨导向系统,将设备故障率降低37%。
二、行业应用场景:从汽车制造到医疗净化
该技术在三大领域展现颠覆性价值:
1. 汽车零部件装配线
某新能源车企的电池包生产线采用双层顶升结构后:
- 上层承载500kg模组完成注胶固化,下层同步回流空板
- 顶升平移机与AGV协同,实现跨楼层物料转运
- 厂房空间利用率提升55%,单位面积产出增加2.1倍
2. 电子产品柔性生产
手机主板组装线的实践验证:
- 静电防护型工装板(表面电阻10⁸Ω)确保芯片安全
- 通过顶升机构快速切换SMT贴片与功能测试工位
- 2小时完成产品换型,支持日产12种型号
3. 医疗无菌车间
制药企业灌装线的创新应用:
- 316L不锈钢链条配合层流罩,满足GMP Class A级洁净度
- 顶升过渡仓设计实现airtight isolation,避免交叉污染
- 灌装精度误差≤±0.1ml,报废率下降至0.02%
三、结构创新:模块化与安全的突破
2025年行业前沿方案呈现两大变革:
• 模组化架构
- 预置300/600/900mm标准节段,拼接误差<0.1mm/m
- 驱动电机接口兼容西门子、三菱等主流品牌
- 控制箱集成Profinet/EtherCAT协议,即插即用
• 本质安全设计
- 嵌入式导轨防护:铝型材包覆链条,仅露出2mm滚轮轮缘
- 双通道互锁:顶升动作触发时,下层自动断电并机械锁止
- 急停响应<70ms,远超ISO 13850标准要求
四、破解行业痛点:成本与效能的平衡术
尽管技术优势显著,企业落地时仍需应对两大矛盾:
空间优化 vs 初期投入
- 双层结构节省40%平面空间,但钢结构支架成本增加25%
- 经济拐点公式:当厂房租金>800元/㎡/年时,18个月内可收回增量投资
柔性生产 vs 维护复杂度
- 模块化工装板支持快速换型,但顶升机构液压系统需每周维护
- 创新油路方案:采用自密封快换接头,维护时间从90分钟压缩至15分钟
五、未来演进:智能化融合的三大方向
我认为下一代技术将聚焦智能感知与绿色运行:
1. 自适应调速系统
通过应变片实时监测链条张力,AI动态调整电机扭矩。某实验室数据显示,该方法可降低17%能耗,延长链条寿命3.2倍
2. 预测性维护网络
滚轮内置振动传感器,结合边缘计算预判故障。实际案例显示,轴承更换周期预测准确率达92%,意外停机减少80%
3. 碳纤维复合材料应用
实验证明:碳纤维滚轮比合金钢减重68%,增速比突破4.2倍极限。但当前成本是钢制件的7倍,量产化仍需工艺突破
自问自答:破解落地难题
Q1:为何汽车厂宁选双层而非环形倍速链?
A: The key is in the重载兼容性与空间效率。环形结构虽维护简单,但:
- 单层承载极限仅300kg,无法满足发动机等重型部件
- 同等产能需多铺35%场地,汽车厂土地成本敏感
Q2:顶升机构如何避免成为系统瓶颈?
A:创新设计解决传统短板:
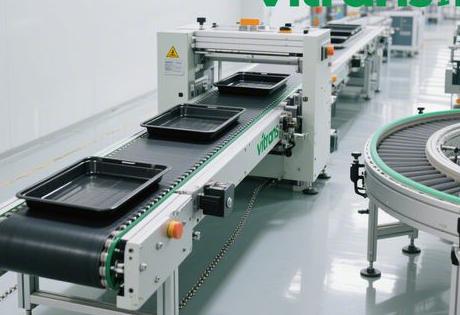
- 双气缸冗余驱动:单缸故障时仍维持75%运行速度
- 滑轨预紧技术:消除间隙振动,定位精度达±0.1mm
- 换向时间<3秒,满足60JPH(件/小时)节拍需求
Q3:哪些场景应暂缓引入此技术?
A:三类情况需谨慎评估:
- 超低速生产线(节拍>5分钟):设备利用率<40%,投资回报率低
- 强酸碱性环境:即便316L不锈钢,在pH<2.5时腐蚀速率倍增
- 微型元件装配:工装板±0.3mm振动幅度可能影响精密作业