###Spatial reconfiguration: an industrial revolution in vertical circulation systems
In a new energy automobile parts factory in Changzhou, a double-layer reflux doubling chain is being used to22 metres per minute.Conveying motor assemblies. Unlike conventional single-tier lines, the upper tier carries fully loaded pallets flowing to the assembly stations, while the lower tier conveys the motor assemblies through theLift and return mechanismEmpty boards will be quietly sent back to the starting point, the formation of a closed-loop system. This vertical layout successfully cracked the manufacturing industry's "space paradox" - Guangdong, a home appliance enterprise transformation case shows that the use of this structure:
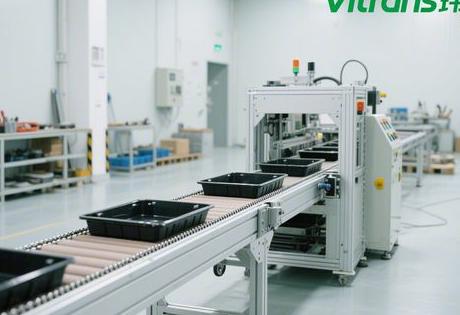
- Site Utilisation Improvement 53%The space was freed up for 3 additional inspection stations.
- Tooling board cycle time compressed from 8 minutes to 4.2 minutes
- Daily production capacity jumps to 28,000 unitsThe failure rate has been reduced by 35%.
The core value lies in the synergistic design of the plate return machine: the cylinder lifts the workpiece plate within 0.4 seconds, and the servo motor drives the rotary platform to complete 90° steering, with the error controlled within ±0.3mm. This "air relay" mode is more efficient than the traditional U-shaped line.Save on 47% FootprintThis is equivalent to achieving 1500m2 capacity in 800m2 of space.
Differential growth rate: the physical intelligence of mechanical structures
#####The kinetic code of the multiplicity chain
At the heart of the double reflux system liesDesign of diameter difference between roller and roller::
make a copy ofPlate speed V = chain speed Vc × (1 + D/d)
When the roller diameter D = 2 times the roller diameter d, the formation of the3x speed effect--An automobile instrument panel production line test shows that when the chain runs at 7.5m/min, the speed of the work plate can be up to 22.5m/min. This design not only reduces the wear of the chain, but also solves the contradiction between high-speed conveying and precise positioning.
#####Precision synergy of reflux mechanisms
Smooth steering requires the precise co-ordination of three major components:
- Jacking unitPressure-resistant cylinders provide a lifting force of ≥1.5 times the safety factor (100kg load requires 1500N output).
- Servo Rotary Stage: Steering accuracy guaranteed by 0.01° indexed absolute encoders
- Orbital Adaptive System: Self-aligning effect of V-groove guides and pallet rollers.
The Suzhou medical device workshop application proved that the system can realise1 turn every 2 secondsThe vibration amplitude is ≤0.05G, which ensures that the precision sensor is not disturbed by vibration.
Industry empowerment: customised breakthroughs in multi-sector scenarios
#####Micron-level control for electronics manufacturing
Shenzhen AMOLED screen production line solves industry pain points through three innovations:
- electrostatic protection and control: Carbon fibre guide wheel + anti-static work plate, surface resistance control at 10⁶-10⁹Ω
- Microvibration isolation: Addition of polyurethane damping pads to the slewing mechanism, reducing amplitude to ±3μm.
- cleanliness guarantee: Ion wind screen integrated at the corner, ≥0.5μm particle concentration <1000pcs/m³
#####The hygiene revolution in food medicine
Innovative solutions for freeze-dried food production lines in Shanghai:
- Material upgrade: Stainless steel chain mirror polishing (Ra ≤ 0.8μm), eliminating microbial residual dead space
- Oil-free design: Slewing mechanism with self-lubricating bearings instead of grease lubrication
- Intelligent SterilisationCIP cleaning nozzles embedded in the jacking platform for automatic daily sterilisation procedures.
The system is FDA-approved and has resulted in a 90% drop in product colony count.
Design Evolution: A Manufacturing Paradigm for Intelligent Convergence
#####Digital Twins Drive Predictive Maintenance
Intelligent system configured by Changzhou Guangliang for BYD's lamp line, deployed in the reflow mechanismVibration-Temperature Composite Sensors::
- Real-time monitoring of 200-1000Hz spectrum to capture bearing wear characteristics
- Temperature difference over 0.8℃ automatically triggers the maintenance programme
- Fault prediction accuracy of 92%Reduction in time-consuming maintenance 70%
#####The Flexibility Revolution in Modular Architecture
The new generation of reflux units in 2025 usesLego-style assembly design::
make a copy ofBasic steering unit (30°/60°/90°) ├── Visual inspection extension port ├── Force feedback adjustment port └── Energy data dual channel
Zhejiang photovoltaic enterprises apply the architecture, only 36 hours to complete the production line restructuring to adapt to the new solar panel size, saving 830,000 yuan in transformation costs.
Manufacturing Process: The Art of Balancing Precision and Efficiency
1. Core parameter design guidelines
- load adaptation: Aluminium alloy rotary disc for light loads (100kg).
- Precision control: Repeatable positioning ±0.2mm, rail clearance = plate width + 3mm (anti-lag)
- Safety RedundancyDual limit switches (mechanical + photoelectric), emergency stop response <0.2 sec.
2. Mass production bottleneck breakthrough programme
Automotive parts factories to solve the problem of conveying long parts:
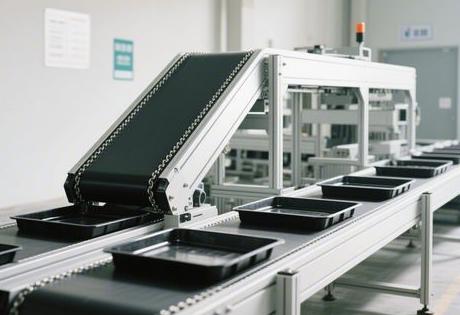
- Three-section telescopic guide: Automatically widens to 2200mm when inducting tooling boards.
- Dynamic Balance System: Side auxiliary wheelset to stabilise 1.8m workpiece during rotation
- Accuracy Guarantee: Docking front rail shrinks to 1850mm, changeover time only 3 minutes
3. Evidence of energy efficiency optimisation
Comparison of measured data from appliance factories:
norm | traditional circular line | Double return chain | optimisation rate |
---|---|---|---|
space occupation | 380 square metres | 210 square metres | 44.7%↓ |
Veneer cycle power consumption | 0.18kWh | 0.09kWh | 50%↓ |
Average daily maintenance hours | 2.1 hours | 0.7 hours | 67%↓ |
Ask yourself the core question.
Q1: What is the irreplaceable nature of the double-layer return structure compared to the traditional loop line?
Space efficiency is a core advantage - a loop requires a 30 metre diameter site to achieve circulation, whereas a double-layer, right-angle layout requires only 12 x 8 metres; and the return mechanism is more efficient than a robotic shift load.Four times faster.The cost is only 1/3.
Q2: How to ensure the stability of reflow in heavy load scenarios?
Programme of an engineering machinery factory: for workpieces over 1000kg, use theSynchronised jacking of two cylinders + crossed roller bearingsThe servo motor torque is increased to 120N-m; the guide rail clearance is controlled at +5mm from the plate width, balancing the need for anti-stallation and precision.
Q3: What is the direction of future technological breakthroughs?
in my viewFusion of superconducting magnetic levitation and speed doubling chainWill trigger a revolution - laboratory verification in -196 ℃ liquid nitrogen environment, the workpiece plate suspension 0.5mm running energy consumption reduction of 87%, which may give rise to the fourth generation of non-contact multiplier chain system, a complete solution to the mechanical wear and tear problem.