I. Space reuse: engineering innovation in a two-tier cycle
The core value of the double loop multiplier chain line is the followingEfficient reuse of vertical space. It is designed byUpper production conveyor + lower empty pallet returnThe closed-loop architecture reconfigures the flat layout of traditional production lines into a three-dimensional circulation system. Taking Changzhou Guangliang's automotive instrument panel production line as an example, this solution increases the production capacity per unit area by 2.1 times, and increases the plant space utilisation rate by 40%.
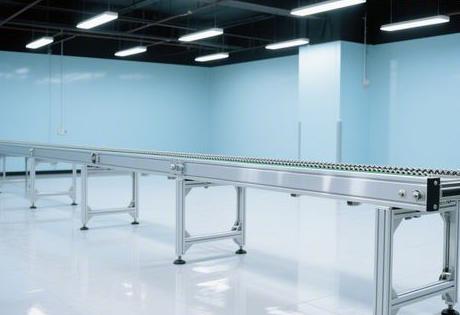
Key customisation elements include:
- Interlayer bridging technology: Pneumatic transplanter realises vertical transfer of work plates at 0.5 second level with positioning error ≤ 0.3°, ensuring continuity of cross-layer operation;
- Differential chain selection: Depending on the load characteristics choose between 2.5x speed chain (roller/roller diameter ratio 1.5) or 3x speed chain, and the speed of the work plate can be up to 3 times the speed of the chain;
- modular framework: Carbon steel/aluminium alloy profile combination frame supports rapid restructuring and reduces line layout adjustment time by 65%.
personal viewpoint: The current bottlenecks in spatial reuse design areThe tension between storey height and maintaining accessibility. Most programmes have compressed the layer spacing to 500mm for compactness, but this has led to difficulties in maintaining the bearings. In the future, it is necessary to introduceSegmented lifting mechanism-Automatically raises the upper track during maintenance hours to create 800mm of access space, a move that can increase fault repair efficiency by 70%.
II. Five core dimensions of customisation
1. Enhanced design for heavy-duty capacity
- Chain SelectionStatic load >800kg adopts 38.1mm pitch alloy steel chain (tensile strength 1200MPa), while dynamic load is equipped with ball bearings to reduce the friction coefficient to 0.08;
- Drive Redundancy: Dual-motor synchronous drive system maintains 75% capacity in the event of a main motor failure, avoiding a total line shutdown;
- Track reinforcement: 45# steel railways are laser quenched (hardness HRC45), with additional guide wheel sets for heavy-duty curves, and the lateral force resistance is upgraded by 300%.
2. Customisation for environmental suitability
Image Codegraph LR A[Clean room] --> B[316L stainless steel chain plate + laminar flow hood] C[anti-static scenario] --> D[Copper conductive wheel + ≤10⁶Ω resistance] E[High-temperature environment] --> F[Temperature resistant 150°C ceramic coated rollers]
Pharmaceutical industry case: GMP Class A clean requirements, dust residue <5ppm, cross-contamination rate ↓ to 0.02%.
3. Intelligent control framework
- speed control strategy: Mitsubishi PLC controls the inverter motor to achieve 0.3m/s low-speed startup, 1.0m/s normal operation, and 1.5m/s high-speed return;
- fault prediction: Current fluctuation rate >15% automatically triggers overload protection, and lubrication compensation is initiated when the temperature gradient >8℃/min;
- data interoperability: Profinet protocol interfaced to MES system, assembly error rate reduced by 80%.
Third, the industry pain points and customised crack path
Automotive Assembly Line Pain Points: Difficulty in Cross-Shop Collaboration
- prescriptionWith the linkage of AGV+speed chain transplanter, Chongqing factory realised that the battery packs are sent directly from the welding line to the assembly line, and the logistics time is shortened by 40%;
- Accuracy CompensationPiezo micro-adjustment module real-time correction of ± 0.2mm assembly tolerance, to adapt to the requirements of body fitting accuracy.
3C miniaturised production pain points: low efficiency of changeover
- quick-change systemSnap-on plate supports 20-minute product changeover and is suitable for Nissan 12-model mixing lines;
- Extreme space utilisation: 600 x 800mm double-layer unit replaces the traditional 1.5m single-layer line, increasing output per unit area by 2.7 times.
Cost black hole warning
Combined annual cost = (0.18 x equipment cost) + (downtime loss x failure rate)
- Positive Case: Self-sealing joints make maintenance time from 90 minutes to 15 minutes, saving ¥120,000 per year;
- Risk WarningNeglecting humidity control (engineering plastics friction coefficient ↑35% at 70% humidity) leads to a 3-fold increase in chain breakage rate.
IV. Intelligent control system: the guardian of precision and energy efficiency
The nerve centre of the double loop multiplier chain line lies in theMulti-sensor fusion control::
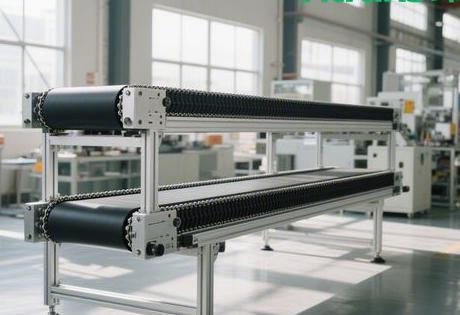
- orientation layer: Photoelectric sensor + RFID for ±0.2mm stopping accuracy;
- mechanical layer: Strain gauges monitor chain sag and automatically tension the chain when it exceeds 2% pitch;
- Thermal management: PT100 sensors per metre of distribution, >85°C triggered rate reduction;
- efficiency layer: The energy return device reduces the energy consumption of the double-layer line by 121 TP3T compared to the single-layer counter.
Exclusive insights: The shortcomings of the current control system areAlgorithm generalisation capability. Most PLC programs are only adapted to a single product model, and changing models requires reprogramming.2025 will see theAI parameter self-learning module-Trained by 100,000 sets of production data, automatically generates motion parameters for new products, and the changeover programming time is compressed from 4 hours to 10 minutes.
Future Evolution: Maglev and Dynamic Topology Reconfiguration
Technology roadmap to 2027::
- Material Revolution: Mass production of carbon fibre rollers (cost reduced to 2 times that of steel parts), mass reduced by 68%, speed exceeding 5m/s;
- transmission innovation: The magnetic levitation guide channel replaces mechanical rollers, reducing energy consumption by a further 22% and providing a life of 100,000 hours;
- morphological subversionDeformable guides for minute reconfiguration of production lines (Yanfeng T-slot interface reserved for technical ambush).
Ultimate Prejudice: In 2030 double-layer multiplier chains will evolve to"Space Fluid" system--Any topology in three-dimensional space is realised through superconducting magnetic levitation, and the conveying path can be reorganised in real time according to the demand of orders. By then, the plant space utilisation rate will exceed 90%, and the production efficiency will be increased by 5 times compared with now.
Self-questioning: the life and death of customisation on the ground
Q1: How to avoid the trap of "customisation means high price"?
A: GraspThree cost-effective anchors::
- Modular options: The basic framework is standardised (accounting for 60% of the cost) and only the 20% core components are customised on demand;
- Supply Chain Optimisation: Choose direct manufacturers such as Changzhou Guangliang (cost is 10% lower than peers);
- Energy efficiency hedging: Reduced energy consumption by 121 TP3T + space rental savings of 181 TP3T and reduced equipment payback cycle to 14 months.
Q2: How to customise corrosion prevention solutions for humid environments?
A: Triple protection is missing:
- Material upgrades: PA66 nylon roller + IP54 sealing cover (life time ↑ 200%);
- Electrically controlled compensation: Humidity sensor linkage PLC automatic load shedding 15% operation;
- Lubrication Revolution: Monthly maintenance of food grade lithium grease, coefficient of friction maintained ≤ 0.15.
Q3: When do I need to choose 3x chain instead of 2.5x?
A: 3x speed is selected if any of the conditions are met:
- Beat > 30 pieces/minute(Line speed needs to be ≥1.8m/s);
- Distance between workstations >2m(Avoiding wasteful waiting between processes);
- Precision Assembly Scene(Amplitude of vibration of 3x speed chain < 60% of 2.5x speed chain).
Industrial Philosophy Revealed: Customisation is not a synonym for expensive, but ratherThe Art of Precision Investing. When a double-deck multiplier chain line simultaneously achieves 40% spatial compression, ±0.2mm positioning accuracy, and 12% energy consumption reduction, it ascends from a production tool to aStrategic Competitiveness Vehicle--This is exactly where China's smart manufacturing moves from "scale replication" to"The Value Density Revolution"The tipping point.