In the intelligent toilet electronic cover assembly workshop, a set of semi-finished parts as if by magic in the assembly line speeding flow. When the work plate slides to the work station three, the mechanical arm falls accurately, and completes the heating film painting in 3 seconds; arriving at the airtightness testing station, the blocker rises noiselessly, the work plate stops steadily, and the robot probe automatically completes the sealing verification -This highly efficient lifeline is the "invisible champion" of modern manufacturing: the speed chain assembly line..
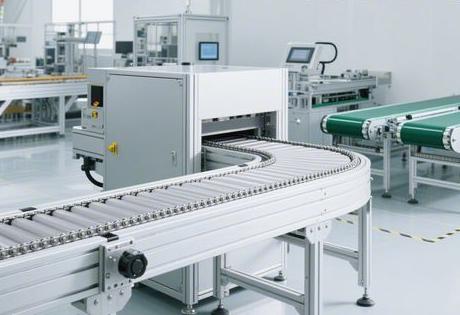
I. Speed Chain Assembly Line: Conveying Engine for Intelligent Manufacturing
Speed chain assembly line (also known as self-flow conveyor system) is the core artery of automated assembly line. Its core principle lies in the special chain structure to achieve "low-speed transmission, high-speed conveying" efficiency multiplier. When the drive motor pulls the chain at a constant speed, the rollers carrying the fixture plate have a speed increasing effect (commonly 2.5-3 times the speed) due to the difference in diameters, so that the fixture plate obtains a conveying capacity beyond the moving speed of the chain itself.
In the Smart Toilet line, this characteristic revolutionises the change:
- Workpiece plate slides at 3x speed in an unobstructed stateReduces workstation transfer time dramatically
- Automatically switches to rolling friction in the event of a stopper.Avoid chain wear
- Decoupling of workstation operations and material handlingThe "run and pause" flexi-tempo is realised.
Second, the key technology composition of the intelligent toilet production line
1. The Faster Chain system architecture
Take a smart cover production line as an example:
- Guideway systems: Adoption of 118 x 100mm aluminium profile guide rail, surface hardening treatment to ensure wear resistance
- transmission core: Triple speed engineering plastic chain made in Suzhou, roller diameter ratio is 1:3.
- Load-bearing design: 40×40mm iron cube frame, load capacity up to 500kg/station.
2. Workpiece return design
Dual-rail circulation structure enables automatic return of empty load boards:
plaintextmake a copy ofUpper production line: the workpiece board loaded with material running → tail off the line → lifting and panning machine transfer Lower level: Empty boards pass through the inclined chute → automatic return to the starting end
The design reduces manual handling by 30% and saves 40% in equipment footprint.
3. Robotics integration applications
- Heated film coating station: Six-axis robotic arm for precise painting of 3D surfaces
- air tightness testing station: Collaborative robot automatically inserts and connects pneumatic fittings, detects leakage of 0.01 ml/min at 0.5 MPa pressure.
- Welding station: Synchronised laser welding of water tank components by four-axis robots
4. Test station integration
Three types of core tests are embedded at the end of the assembly line:
- Ground conductivity test: 1000V withstand voltage test
- Full-featured aging test: 72 hours of continuous load operation
- Flow Calibration System: Dynamically adjusts water parameters to ±2% accuracy.
The test data is bound to the product barcode in real time and is traceable for ten years.
Third, the design points of the doubled speed chain assembly line
1. Golden rule of chain selection
Load Type | Recommended Chain Types | Applicable Scenarios |
---|---|---|
<20kg | Single Speed Chain | Assembly of electronic components |
20-80kg | 2.5x speed chain | Cover part assembly |
>80kg | Triple speed chain + steel rollers | Complete machine test station |
2. Precision control of the guideway system
- Straightness error ≤0.5mm/m
- Horizontal deviation <0.3mm/m
- Bend radius ≥ 3 times chain pitch (76.2mm standard)
3. Driver configuration specifications
matlabmake a copy ofMotor power formula: P = μQv/(η*)1000) // μ coefficient of friction (from 0.2 to 0.3) // Q Total load (kg) // v linear velocity (m/s) // η mechanical efficiency (0.85)
In practice, a double sprocket synchronous drive is used, together with a 1:30 reduction gear to ensure smooth starting and stopping.
4. Stowage control innovations
pass (a bill or inspection etc)Pneumatic stopper + photoelectric sensingEnabling dynamic regulation:
- Automatic accumulation of pallets when the workstation is fully loaded.
- Automatic upstream cut-off in case of abnormal shutdown
- Autonomous release of the backlog of workpieces after resumption of operation
This technology has increased line efficiency by 271 TP3T and reduced downtime by 601 TP3T.
IV. Industrial change driven by multiplier chain technology
In a smart toilet factory in Taizhou, Zhejiang, the speed chain assembly line brings subversive changes:
- Productivity leap: 8-20 station flexible configuration increases daily capacity from 800 to 2400 units.
- Revolutionary breakthrough in compatibility: 20 different types of covers can be mixed in the same production line, with a switching time of <3 minutes.
- Quality Traceability Enhancement: MES system binds test data through barcode of workpiece board, defect rate reduced to 0.12%
Of even greater concern is the fact thatMultiplier chain systems are being deeply integrated with digital twin technologyA head enterprise built a predictive maintenance model by collecting parameters such as chain tension and bearing temperature and motor current in real time. A head enterprise has constructed a predictive maintenance model through real-time collection of parameters such as chain tension, bearing temperature, motor current, etc., so that the sudden failure rate of the equipment has dropped by 751TP3 T. This mode of "physical transport + digital mirror" will become a new standard for intelligent factories.
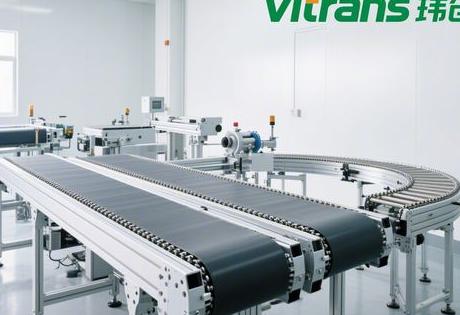
V. Future Manufacturing: Beyond Multiplying Evolutionary Paths
As I stood watching at the end of the assembly line, I realised that the value of the multiplier chain goes far beyond speed itself - it is essentially theReconfigures the spatial logic of production relationsThe traditional assembly line binds the worker to a fixed position. While the traditional assembly line binds workers to a fixed position, the accumulation and release function of the Speed Chain allows workers to adjust their own pace. This "human-machine adaptability" provides a humanised upgrade path for the factory of the future.
As the cost of modular robots falls, we foresee a new shape for the next generation of production lines.Conversion of the speed chain orbit into a "power + data" dual-rail systemIn addition, the work plate is upgraded to an intelligent AGV carrier, which can achieve three-dimensional spatial reorganisation while maintaining three times the speed of conveyance. When this flexible manufacturing network is combined with the AI scheduling system, the production beat of the smart toilet will break through the linear limitations and move towards the real "unconstrained manufacturing".
Comparative Line Performance Data
Conventional belt line: conveying speed 0.3m/s, switching stations takes 15 seconds.
Speed chain system: conveying speed 1.2m/s, workstation blocking response ≤ 0.5 seconds.
Self-questioning: a breakdown of the core issues
Q1:How is the "multiplication" of the speed chain realised?
Leverage effect is generated through the difference in diameter of the small and large rollers. When the chain drives the small roller (diameter d) to rotate, the large roller (diameter 3d) on which the workpiece plate depends travels 3 times the distance in the same time, realising 3 times the speed of conveying.
Q2: Why do I need the accumulation function for smart toilet production?
Airtightness testing requires 120 seconds of constant pressure, and function testing takes 3 minutes. The accumulation function allows specific boards to stay in operation while other boards continue to flow, preventing the entire line from coming to a standstill.
Q3: What is the biggest difference between Speed Chain and normal conveyor line?
centreSeparation of drive and conveyor speedsTraditional conveyor line start-stop is the whole line start-stop. Traditional conveyor line start-stop is the whole line start-stop, but the speed chain can realise the flexible control of "local stop, global flow".