Why Vertical Conveyor Lines are the throat equipment of modern logistics?
Vertical conveyor lines (hoists) are automated hubs that connect different floors or heights through theContinuous vertical handlingReplacement of traditional freight elevators forSegregation of people and goods for safe operationtogether withSeamless system integrationThe core value is: save 70% floor space, improve efficiency (up to 3000 pieces/hour). Its core value lies in: saving 70% floor space, improving the conveying efficiency by more than 3 times (up to 3,000 pieces/hour), and adapting to complex scenarios such as cold chain, explosion-proof, and clean. If its role is ignored, enterprises will face three major pain points.Lagging efficiency of manual handling(For example, the efficiency of freight elevator operation at the Boyang Logistics Centre is only 61 pallets/hour).Waste of space resources(New energy plant material flow path is complicated)Risk of quality fluctuations(Wear and tear of materials due to manual handling in the home furnishing industry).
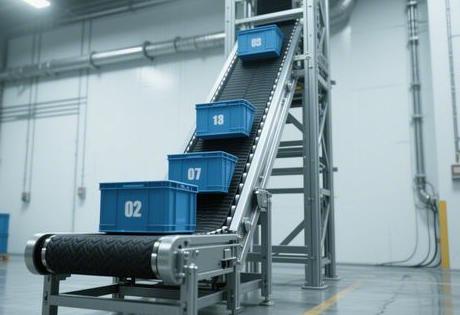
Apparel Logistics: How Boyang Group breaks through the distribution bottleneck of 1600 shops?
challenge: Under the mixed structure of flat storage and floor storage, the traditional freight elevator is inefficient (61 pallets/hour) and requires special equipment reporting, which slows down the response speed during peak seasons.
prescription: Retrofitting in existing goods lift shaftsReciprocating Vertical Conveyor Systems, key parameters:
- Load 600kg/pallet, speed 35m/minute
- Configuration of heavy-duty drum machine + intelligent control system, support for automatic / manual / maintenance of three-mode switching
- Import and export docking hydraulic forklift trucks for seamless pallet transfer.
efficacy: Cross-floor handling efficiency increased by 40%, manpower costs decreased by 30%, and 22 million pieces of bedding are handled annually without pressure.
What happens if it is not upgraded?
The average daily handling capacity of traditional freight elevators is less than 1/3 of the automated system, and delivery delays to 1,600 shops will result in over 15% of peak season orders lost.
New Energy Manufacturing: How an EV brand doubled its production capacity?
sore pointHuizhou production base is facing three major problems: production line beat imbalance, complex material flow path, and poor assembly consistency.
The Key to Breaking the GameDeployment of 65 setsVertical Conveyor SystemsTo build a three-dimensional logistics network:
- Finished products are connected to the first floor of the intensive warehouse via vertical conveyor, and the WMS system dynamically optimises the storage path.
- Modular grading of aftermarket spare parts: unitised conveyance of bins → intelligent sorting of cartons
- Linked with 380 sets of chain machines and 205 sets of transfer machines to form an intelligent conveying matrix.
results-based:: - The average daily inbound and outbound volume of finished trucks exceeded the capacity limit.
- Warehouse manpower reduced by 50%, material wastage rate reduced by 35%
- Storage capacity utilisation increased by 40%, saving storage space.
Industry Insights: New energy production lines need to be matchedExplosion-proof Vertical Conveyor(Zinc-nickel-copper materials are prohibited) to avoid safety hazards in the handling of battery materials.
Smart Home: How to overcome the difficulties of customised production of high-end mattresses?
transition dilemmaA healthy sleep brand is facing a surge of small-volume custom orders, the original production line can't be flexibly switched, and the order delivery cycle is extended by 30%.
Intelligent Conveyor Solutions::
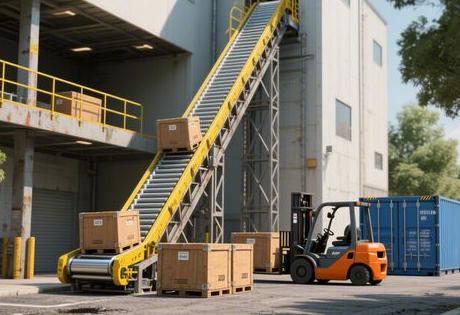
- Three-dimensional U-shaped production line designVertical conveyor line connects cutting, sewing, stuffing and more than 10 other processes, freeing up flat space.
- Single-piece conveyor systems: Global efficiency ≥ 480 pieces/hour, end docking truss manipulator to complete high precision filling
- Dynamic dispatch system: WCS binds order information to achieve "staggered production" of standard and customised mattresses.
A leap in effectiveness: Daily production capacity increased by 25%, manpower cost decreased by 40%, and material wastage rate was close to zero.
Lessons from failure: Local automation transformation if the lack of vertical conveying hub, will lead to process connection fault - a company because of the lack of deployment of the connection system, the robot idle rate of 50%.
Pharmaceutical distribution: how Shanxi pharmaceutical enterprises to ensure the safe transit of tonnes of raw materials?
demanding: Safe conveying of 1.5 tonnes of pharmaceutical raw materials within a head of 18.75 metres and meeting GMP cleanliness standards.
Innovative applications: AdoptionFour-way vehicle + layer-changing hoistIntegrated programmes:
- Vertical conveyor car is equipped with laser positioning device, positioning accuracy ±1mm.
- Top equipped with dual closed-loop control system for fall prevention (laser distance measurement + encoder)
- Millisecond response to signal interaction with the shuttle, with mandatory safe locking of the lifting process.
industry benchmark: 3 systems to achieve a daily average of 1,500 tonnes of raw materials transferred across floors with zero accidents.
Selection Warnings: a must for the pharmaceutical industryStainless steel + anti-static moduleThe ordinary carbon steel equipment is prone to condensation and contamination of drugs at low temperatures.
The Golden Rule of Cross-Industry Selection
A four-dimensional decision-making model based on more than a thousand cases:
dimension (math.) | Apparel/e-commerce | new energy | Pharmaceutical/Food |
---|---|---|---|
efficiency | >1000 pieces/hour | >150 torr/hour | >80 torr/hour |
carrying capacity | ≤100kg (box) | 5 tonnes (pallet) | 1.5 tonnes (shelves) |
environmental adaptation | Normal temperature + low noise | Explosion-proof + anti-corrosion | Clean + Cold |
Accessibility highlights | AGV + roller line | RGV + chain machine | Four-way cart + shuttle board |
experience acquired through blood and tears: Boyang Logistics saved 20% transformation costs by retaining part of the freight elevator as a backup; while a food factory blindly chose a high-speed spiral machine without considering the humidity of the barrels of water, resulting in chain corrosion and downtime -Flexible Configuration + Scenario PreviewThat's the key to success.
The value of a vertical conveyor line is not in the parameters of a single machine, but in theHow to bite the global logistics gear. When Ningbo power plant with 48 sets of continuous hoist tandem production line, efficiency exceeded 600 boxes / hour behind the redefinition of the "vertical space is productivity" - the real intelligent logistics, starting from the absolute control of the three-dimensional dynamic line.