## I. Engineering Wisdom for a Three-Dimensional Cyclic Architecture
Double loop multiplier chain passes throughVertical space reuse technologyReconfiguring the layout of the production line is centred onClosed-loop design of upper production level and lower return channel::
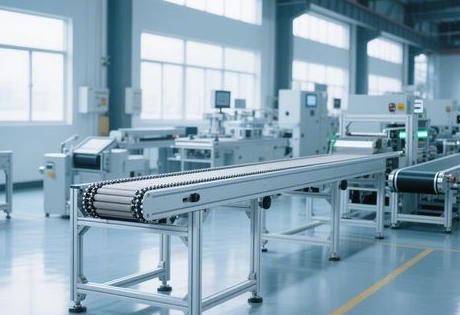
- upper transport layer: Carrying pallets to perform assembly tasks, compressed to 2.5 metres between stations, supporting parallel operation of multiple processes.
- Lower Return Channel: Empty tooling boards are vertically transferred to the lower level by a loader, eliminating the 40% invalid stroke and avoiding cross-congestion on the production line.
- Dynamic speed control mechanism: Realisation of the multiplier effect based on the diameter difference between the roller (D) and the roller (d) (Eq.v = v₀ × (1 + D/d)), which enables the speed of the workpiece to be 2-3 times the speed of the chain.
Industry ValidationAfter adopting this structure for Great Wall Motor's instrument panel production line, the footprint has been reduced by 37.5%, the density of workstations has been increased by 25%, and the annual production capacity has exceeded 180,000 units.
## II. Synergistic technologies for core components
1. Precision docking of loaders
- vertical transferCylinder drive + double linear guide, repeatable positioning accuracy ± 0.1mm, air pressure fluctuations need to be ≤ 0.1MPa
- Anti-collision design: RFID positioning module real-time calibration of the position of the workpiece board, error>0.5mm trigger emergency stop
- Energy consumption optimisationServo regenerative braking technology recovers falling potential energy, energy saving rate ≥15%
2. Intelligent control of blocking mechanisms
typology | Applicable Scenarios | technological breakthrough |
---|---|---|
Pneumatic Horizontal | Heavy duty (500kg load) | Adaptive air pressure adjustment for anti-jamming |
Electric Vertical | Precision assembly (response 0.3s) | Piezo-ceramic sensor detects micron-scale offsets |
Golden Rule: Stopper gap is strictly controlled at 0.1-0.3mm - too tight leads to speed doubling failure, too loose triggers positioning excessively poor |
3. Modular extension interface
- AGV docking port: Reserve standardised interfaces to reduce late modification costs 30%
- robotic coordination: Pre-embedded positioning fiducials on the tooling plate, guiding the robotic arm to grasp with ±0.05mm precision.
## III. Industry-tailored practical programmes
1. Electronics manufacturing: anti-static and high precision
- electrostatic protectionEngineering plastic chain + conductive wheels (resistance ≤ 10⁶Ω), plus anti-static coating when humidity > 70%
- vibration suppressionServo closed-loop control + S-type acceleration and deceleration curves (acceleration ≤ 0.5m/s²), patch offset rate down to 0.05%
2. Automotive heavy industry: heavy loads and synchronisation
- Hardened alloy steel chain: 2 tonnes at a single point, temperature resistant to 600°C
- long-distance deflection proofingDual motor drive + laser alignment instrument, solving the problem of 40m long line runout, the failure rate down 60%
3. Food and pharmaceutical industry: clean compliance
- Dead-angle free structure: 316L stainless steel chain + fully sealed cover, resistant to alcohol rinsing
- Zero-contamination lubrication: FDA approved self-lubricating bearings, maintenance-free cycle > 500 hours
Performance Comparison::
- 40% increase in space utilisation over single level loops
- Energy consumption is 28% lower than traditional drum line, and the cost is only 20% for maglev system.
## IV. The Golden Rule of Selection and Design
Law 1: Load-material matching model
- overloaded scenario(>1 tonne): 3x speed chain is prohibited! Preferred 2.5x speed chain + hardened steel rollers (lower risk of chain breakage when overloading 30% than 50%)
- High speed with light load: 3x speed engineering plastic chain, carbon fibre reinforced for 3x longer life
- special environmentDusty conditions plus sealing cover, wet environment with lithium-based water-resistant grease (100 ℃ viscosity ≥ 46mm ² / s)
Law 2: Balancing cost and efficiency
Image Codegraph TD A[Needs analysis] --> B{Space limitations?} B --Height of plant<5m--> C[Compact double-decker layout] B --- Plane Sufficiency --> D[Single-layer ring programme] C --> E[Drive system selection] D --> E E -- overloaded scene --> F[2.5x speed chain + dual motors] E -- light duty high speed --> G[3x speed chain + servo inverter]
(Source: Industrial Automation 2025 White Paper)
Early warning of hidden costsNeglecting the self-lubricating design will result in an increase in annual maintenance costs of ¥80,000/km.
## V. Three Evolutionary Directions for Intelligent Upgrading
- Digital Twin Surveillance
Roller embeddingMicrostrain SensorsReal-time early warning of overload risk (error rate <5%), a home appliance company applied to reduce downtime by 40%.- Hybrid Drive Architecture
- Basic conveying: conventional motors guarantee continuous operation
- Precise positioning: integrated linear motors in the jacking mechanism, precision jumps to the micron level.
- Adaptive Speed Ratio
Hydraulically adjustable variable-size rollers, in-line switching 2.5X/3X times, reduced changeover time 80%Exclusive Prejudice: In 2028, there will be a "chain-machine symbiosis" - speed chain directly embedded in the drive motor, the cancellation of the mechanical transmission chain, energy consumption down 35%, but need to break through the permanent magnet temperature > 200 ℃ technology Bottleneck
## Self-questioning: engineering the core questions on the ground
Q1: Why is 3x chaining banned in automotive factories? But electronic factories apply it?
A: 3x chain ofLarger roller-roller diameter ratioWhen the load is heavy, the stress is concentrated at the articulation point of the chain plate. Measured data: When the load is over 30%, the risk of chain breakage of 3xspeed chain is 50% higher than that of 2.5xspeed chain; the workpiece of electronic factory is usually less than 50kg, while the automotive parts are often more than 1 tonne.Q2: How to solve the vertical transfer positioning deviation?
A: Three-dimensional calibration strategy:![]()
- pressure regulation in air circuit(Fluctuation ≤0.1MPa)
- Guideway Alignment(Parallelism error <0.05mm/m)
- Servo Valve Replaces Solenoid Valve
Q3: Can modular retrofitting really reduce costs?
A.Short-term investment increase 10%, long-term cost reduction 30%--Modularity makes the workstation transformation cost <¥30,000, downtime reduced to 8 hours, the traditional transformation needs ¥150,000 + 3 days downtimeQ4: How to avoid lubrication contamination in food line?
A: Triple protection:
- physical isolation: Stainless steel labyrinth seal ring
- chemical substitution: FDA approved grease (water content <500ppm)
- Intelligent monitoring: Real-time early warning of oil and grease moisture content